5 Points To Consider Before Selecting Self-Cleaning Magnetic Separators
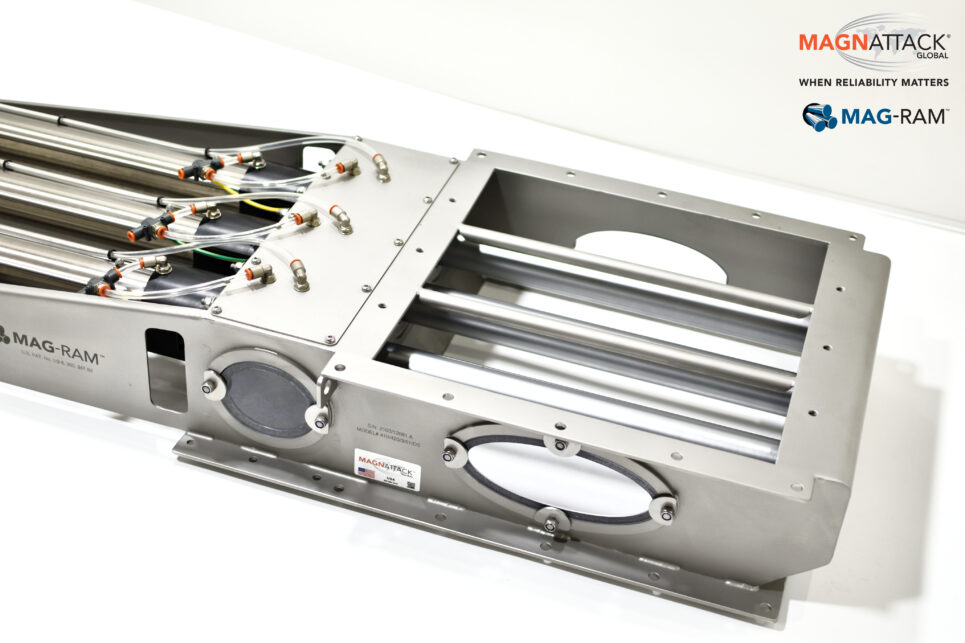
When it comes to the cleaning operation, magnetic separators can be distinguished into two main categories:
1.Self-cleaning separators (also known as ‘auto-clean magnetic separators’), and
2.Manual clean separators.
While manual-clean magnets may be less expensive in the short-term, to many food processing companies this is far outweighed by the advantages of automatic magnetic separators.
Before installing an automated self-cleaning magnetic separator in your process line, there are 5 important points to take into consideration:
1. Reliable cleaning operation and function
It is important that the magnet can withstand the demands of each specific duty, such as product that is abrasive, sticky, or dusty. Over the long term, these factors can be adverse to the cleaning function and eventually lead to failure or the magnet becoming a contamination risk source itself.
Points to consider:
-Moving parts are safe, sealed and protected from external elements
-There are no unhygienic cavities potentially exposed to the product flow area (e.g. sleeved magnets)
-Uneven wear on seals and moving parts causes excess friction which can eventually lead to risk of jamming and incomplete cleaning cycle
-Misalignment of an individual magnet can hinder the entire magnet row from retracting
-Cost of ongoing maintenance
-Availability of replacement components to avoid costs and downtime associated with specialized service technicians time on site
2. Evaluate restriction to product flow
A magnetic separator will inevitably disrupt the product flow to achieve necessary product coverage. This is crucial to successful separation of magnetic fines contamination and needs to be achieved without compromising throughput capacity.
Product flow is influenced the most by speed, height, density, and moisture levels. This can be controlled by adjusting the open area ratio or varying the cleaning cycle frequency when designing the magnet.
Other features can be engineered into the magnet such as rotating each individual magnet to agitate the flow and dislodge non-magnetic build-up, as well as using the patented Dura-Slik® surfacing treatment to reduce surface tension and excess residue build-up on the magnet surface that could potentially lead to bridging and blockage.
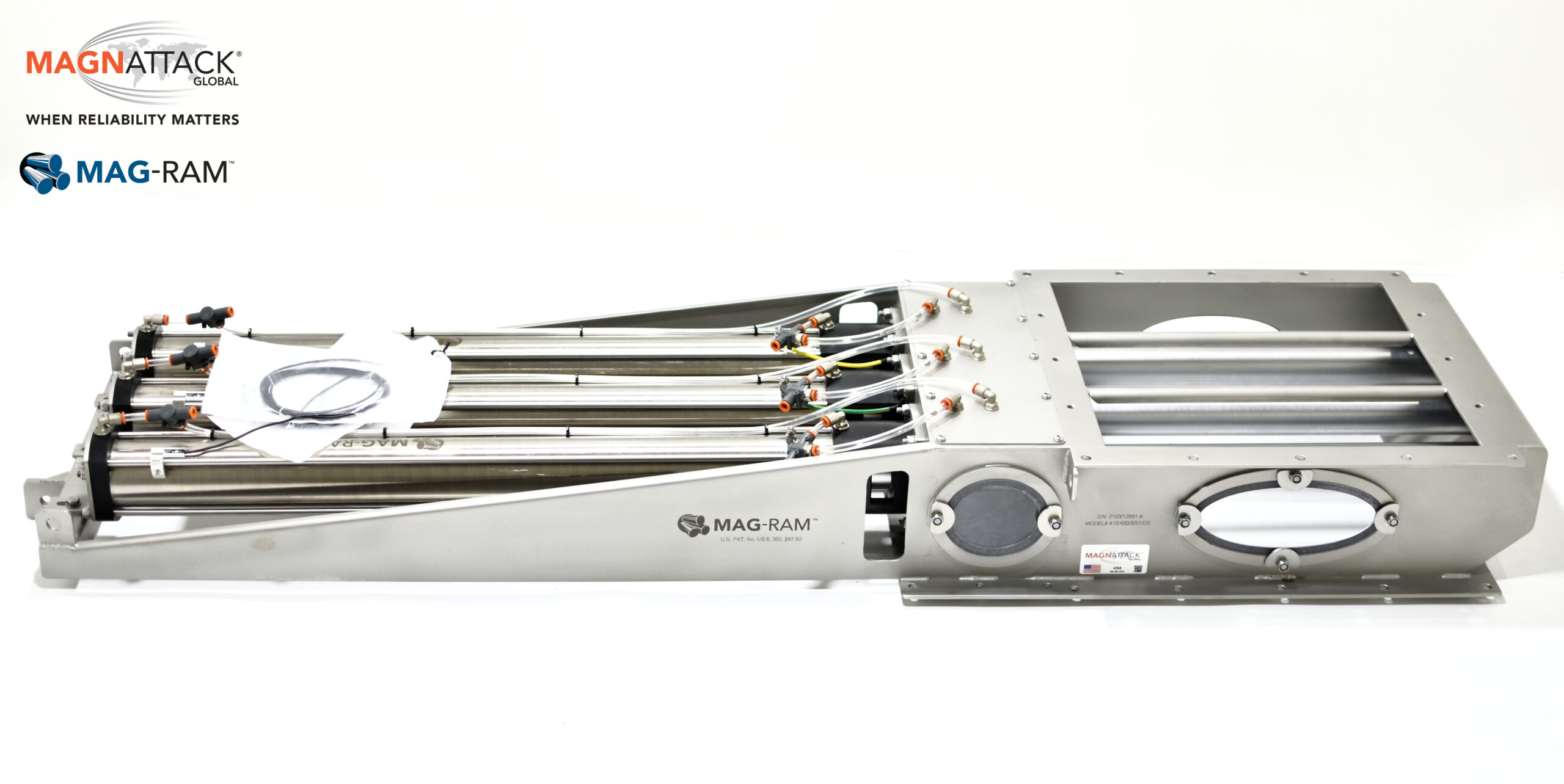
3. In-stream cleaning capability
In most applications, the product stream needs to be paused while the cleaning takes place. This reduces risk and optimizes product coverage, however, with a carefully controlled cleaning programme, it is feasible to ensure protection of the product stream during the self-cleaning cycle.
A self-cleaning separator that can be cleaned during production runs is beneficial in that:
-Maintained production = less downtime and increased productivity
-It provides the advantage of maintaining production capacity in a continuous product stream
-Clean magnets are consistently presented to the product flow. A clean magnet = an efficient magnet = increased food safety
-There is no need for operator intervention or ingress to the product stream. Valuable for sanitary product lines.
4. Using Stand-Alone Controls vs PLC connection
Ideally, the self-cleaning magnet should be integrated into your PLC or SCADA system. This means that you can have all signals and timing control settings back to the central command for production. The sensors and switches will provide information to ensure the magnet is always in stream for maximum protection.
Integration to existing PLC is not always an option. You should consider a stand-alone timing control system that provides the necessary adjustment needed to meet the specific contaminant yield for each application. This is especially important for magnets installed in difficult to access or high-risk locations as it reduces WHS risks involved with accessing these magnets for cleaning.
5. Product Wastage and Excess Product Carry-Over
A lean contaminant sample is desired for optimum traceability and quantifying of fragment contamination. If the product contamination is not minimized, there will be a bulk product wastage carried over to the contamination chamber. This makes the contaminant sample very difficult to analyze and is a big cost in high value materials.
At the design phase of your project, you need to consider the benefits of:
-Rotational indexing of each magnet to remove the pyramid of product build up on each bar
-Calibrated air stream curtain to reduce carry over to contaminant chamber
-Pressurized chamber to reduce carry over and loss of product
-Frequency of cleaning
-Correct type of tight-fitting wiper seals
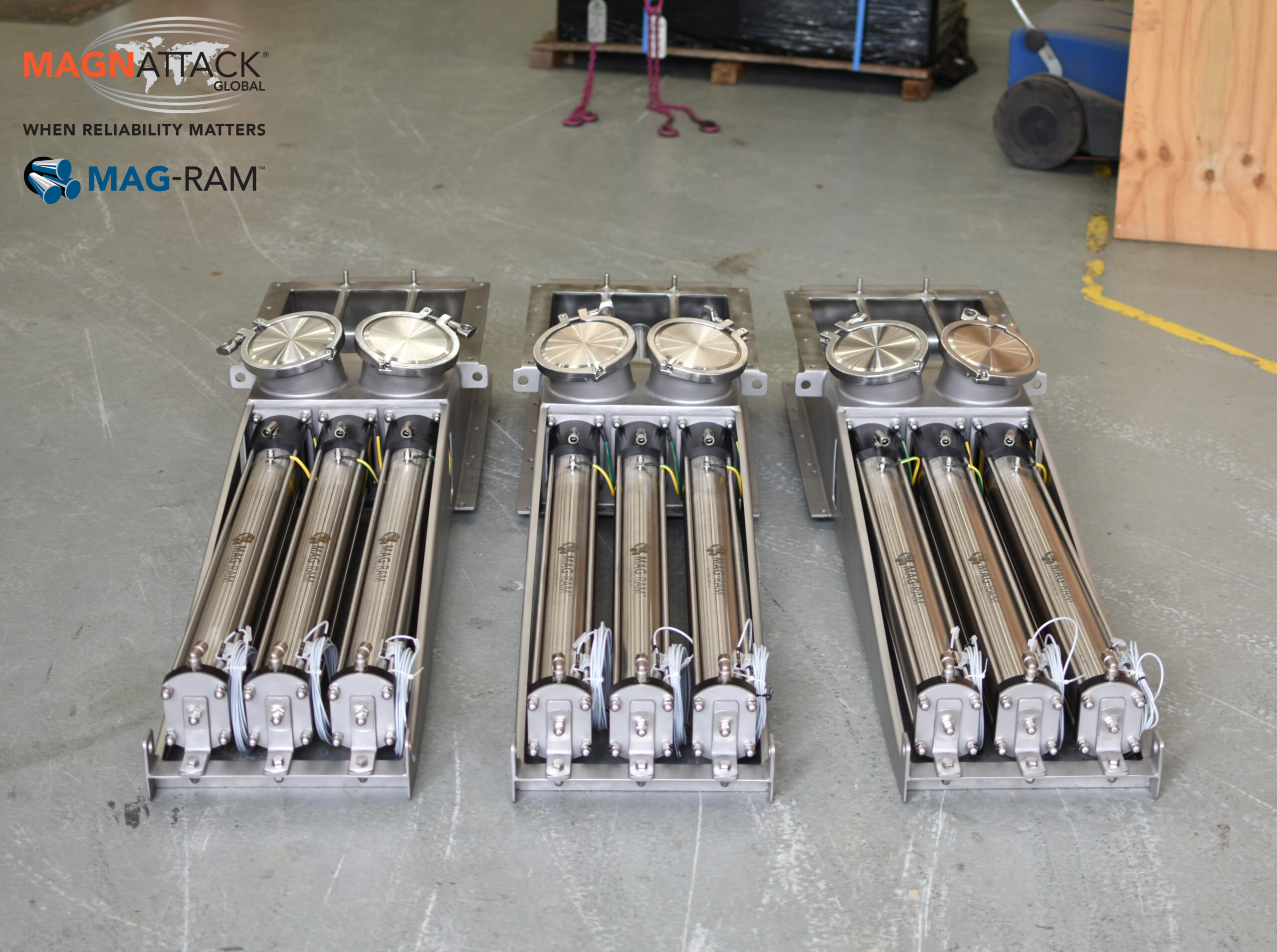
Conclusion
These are the 5 points that you can ask your magnet supplier to assist you in making an informed decision. Each application is unique, and the separation efficiency must be considered for each application using available data.
Selecting a magnetic separator that is not adequate for your process line can result in unreliable cleaning and inefficient metal fragment control and can leave your final product at risk of metal contamination.
Magnattack® Global has developed the RE80® +11,000 Gauss Mag-Ram® Self-Cleaning Separator, which is engineered to provide continuous, sanitary, and efficient magnetic separation for some of the most challenging applications. Learn more about the Mag-Ram® here or talk to a Magnattack® technician today.
Magnattack® Global – When Reliability Matters.