Choosing the Right Dairy Processing Equipment
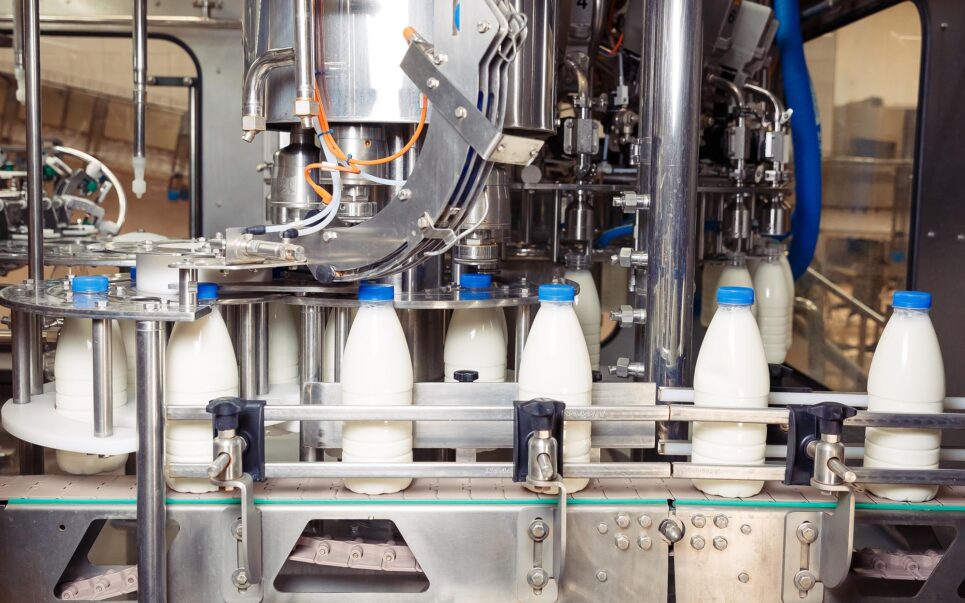
From the cow to the customer, dairy processing equipment can make or break your product’s quality. Finding the right equipment is the ultimate key to maintaining your quality standard.
However, there are some unsung heroes that will help bolster your product’s quality and safeguard your reputation: magnetic separators.
Choosing the Right Dairy Processing Equipment
Selecting the appropriate equipment for dairy processing is essential to ensure optimal performance, hygiene, and compliance with food safety standards. Here are the key considerations to keep in mind:
Sanitary Design
Sanitary design is critical in dairy processing to prevent bacterial growth and ensure product purity. The equipment should feature smooth surfaces and no crevices where product particles can accumulate and bacteria can grow. It should be easy to clean and constructed from materials that do not harbor bacteria. Look for equipment designed with sanitary considerations in mind, such as smooth welds, rounded edges, and easy disassembly for thorough cleaning. This ensures that the equipment maintains a high level of hygiene and reduces the risk of contamination.
Compliance
Compliance with food safety standards is a must. Ensure that the equipment meets USDA Dairy specifications, HACCP (Hazard Analysis Critical Control Point) guidelines, and other relevant international standards. These certifications indicate that the equipment has been designed and manufactured to meet rigorous food safety criteria. Compliance ensures that dairy processing plants meet regulatory requirements, avoid penalties, reduce the risk of recalls, and maintain consumer trust by delivering safe and high-quality products.
Ease of Cleaning
The cleaning process should be straightforward, sanitary, and minimally intrusive to the product zone. This is crucial to maintain hygiene and reduce downtime. Equipment designed for easy cleaning will often feature quick-release components, accessible surfaces, and CIP (Clean-In-Place) capabilities. These features allow for thorough and efficient cleaning, reducing the risk of contamination. Ensuring ease of cleaning is particularly important in dairy processing, where hygiene standards are exceptionally high.
Durability
Durability is essential for long-term performance and reliability. Dairy processing equipment should be constructed from robust materials such as stainless steel, which is resistant to corrosion and can withstand the rigors of the processing environment. Equipment that maintains its integrity over time reduces maintenance costs and minimizes downtime due to repairs or replacements. Investing in durable equipment ensures consistent performance and a longer operational lifespan, contributing to overall cost savings and efficiency in dairy processing.
Efficiency
Efficiency in dairy processing equipment is crucial to ensure that the production process is smooth and cost-effective. The equipment should be designed to handle the specific requirements of dairy products, such as maintaining appropriate temperatures, ensuring consistent mixing, and preventing product loss. Efficient equipment reduces waste, improves product quality, and increases throughput. Features like automated controls, energy-saving mechanisms, and high-capacity processing capabilities contribute to the overall efficiency of the dairy processing operation.
Additional Considerations
- Versatility: Equipment should be versatile and capable of handling various dairy products, including milk, cheese, yogurt, lactose powders, infant formula, and butter. Versatile equipment reduces the need for multiple machines, saving space and costs.
- Scalability: Consider the equipment’s scalability. As your dairy processing operations grow, the equipment should be able to accommodate increased production volumes without compromising on performance or quality.
- Maintenance and Support: Ensure that the equipment comes with robust maintenance and support services. Reliable technical support and easy access to spare parts are crucial for minimizing downtime and ensuring the smooth operation of the processing line.
By considering these key factors, dairy processors can select the right equipment to ensure product safety, enhance efficiency, and comply with stringent food safety regulations. Investing in high-quality, durable, and efficient equipment tailored to the specific needs of dairy processing operations is essential for delivering safe, high-quality dairy products and achieving long-term operational success.
Integrating Magnetic Separators into Your Process
Don’t let magnetic separation equipment intimidate you. Here are some helpful tips for seamlessly integrating it into your existing operations.
Assessing Your Needs
Before integrating a magnetic separator, assess your plant’s specific needs. Identify critical points in your process where metal contamination is likely to occur or needs to be prevented from remaining, such as incoming ingredients, processing equipment discharge, and packing lines.
Installation and Maintenance
Ensure proper installation of the magnetic separators at identified critical points. Regular maintenance and validation of the magnets are crucial to maintaining their efficiency and compliance with food safety standards.
Monitoring and Optimization
Continually monitor the performance of your magnetic separators. Analyze collected contaminants to identify potential sources of metal fragments and take corrective actions. Regular audits and risk assessments can help optimize performance and ensure ongoing compliance with safety standards.
Like any good dairy processing company, your company should stay ahead of possible threats to product quality. By understanding the origins of metal contamination in dairy processes, you can be proactive.
Magnattack’s Solutions
Magnattack offers a range of magnetic separators designed specifically for the dairy industry. Here are some of their key products:
Mag-Ram® Automatic Self-Cleaning Magnet
The Mag-Ram® is ideal for spray dryers or bulk powder packing applications. It features an automatic self-cleaning mechanism, eliminating the need for manual cleaning and reducing the risk of contamination. The absence of stainless-steel sleeves prevents product build-up, ensuring a hygienic operation. USDA-Accepted models available:
Rapidclean® Grate Magnet
This magnet is perfect for dry food product lines. It allows for safe and effective manual cleaning, with the ability to collect and analyze findings outside the product stream. This reduces recontamination risks and enables visual inspection of the bars before returning them to the product flow area. USDA-Accepted models available.
Emulsion & Slurry Pipeline Separator
Designed for thick and viscous liquids, this separator features Acutex® Probe Magnets that ensure minimal resistance to flow and smooth product transition. It effectively captures metal fragments without causing leaks, blockages, or pressure problems. USDA-Accepted models available.
Powder Transfer Magnet
A highly sanitary pneumatic transfer magnet featuring Acutex® Probe Magnets configured to remove even the smallest and weakly magnetic fragments (including work-hardened stainless steel fragments) in high-velocity pneumatic convey lines. USDA-Accepted models available.
Benefits of Using Magnattack Magnetic Separators
There are some definitive advantages to adding magnetic separators to your processes, including:
Improved Product Safety
Magnattack’s separators effectively remove metal contaminants, ensuring the highest levels of product safety. This reduces the risk of recalls and enhances consumer trust.
Cost Savings
By preventing equipment damage and product recalls, and reducing downtime, Magnattack’s magnetic separators lead to significant cost savings. These high-quality magnetic separators are built to last!
Regulatory Compliance
Magnattack’s products are designed to meet international food safety standards, providing dairy processors with the assurance that their operations are compliant with regulatory requirements.
Enhanced Efficiency
With features like self-cleaning mechanisms and easy maintenance, Magnattack’s separators improve overall process efficiency, leading to smoother operations and higher productivity.
Level Up Your Dairy Processing With Magnattack Magnetic Separators
Integrating Magnattack magnetic separators into your dairy processing plant can significantly enhance product safety, process efficiency, and regulatory compliance. By carefully selecting and maintaining the right dairy processing equipment, dairy processors can minimize the risks of metal contamination and ensure the highest standards of quality and safety. Contact us today for a free consultation.