Improving Meat Meal Value & Increasing Profitability Through Contaminant Reduction
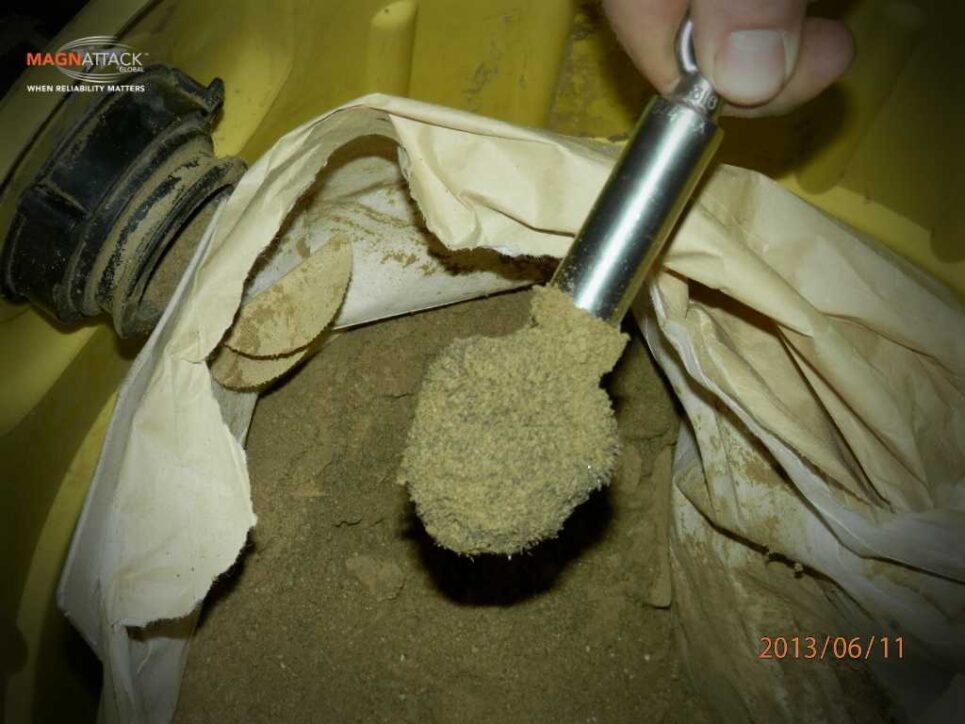
Foreign contaminants, such as plastic and metal, can have a huge impact on the value of meat meal if they are found in the final product. In order to maintain customer confidence and increase product value, the contaminants must be removed.
Magnetic separation is a proven method of removing metal fragments from product lines, however, there are two main hurdles that renderers face:
- Very fine wear iron and weakly magnetics
- Ineffective magnet systems
Fine Wear Iron And Weakly Magnets
Efficient separation of very fine metal contamination is a well-known challenge in meat meal, due to being lower in magnetic mass and often weakly magnetic such as stainless-steel grades. Meat meal processing is considered a high impact process that will introduce continuous wear iron over time. These fragments are introduced via processing equipment such as hammer mills, screens, trough wear, and other moving parts.
If effective separation of these tiny fragments is not achieved, there is a high risk that it will become a serious product security issue for the business, especially to meet pet food grade or export requirements.
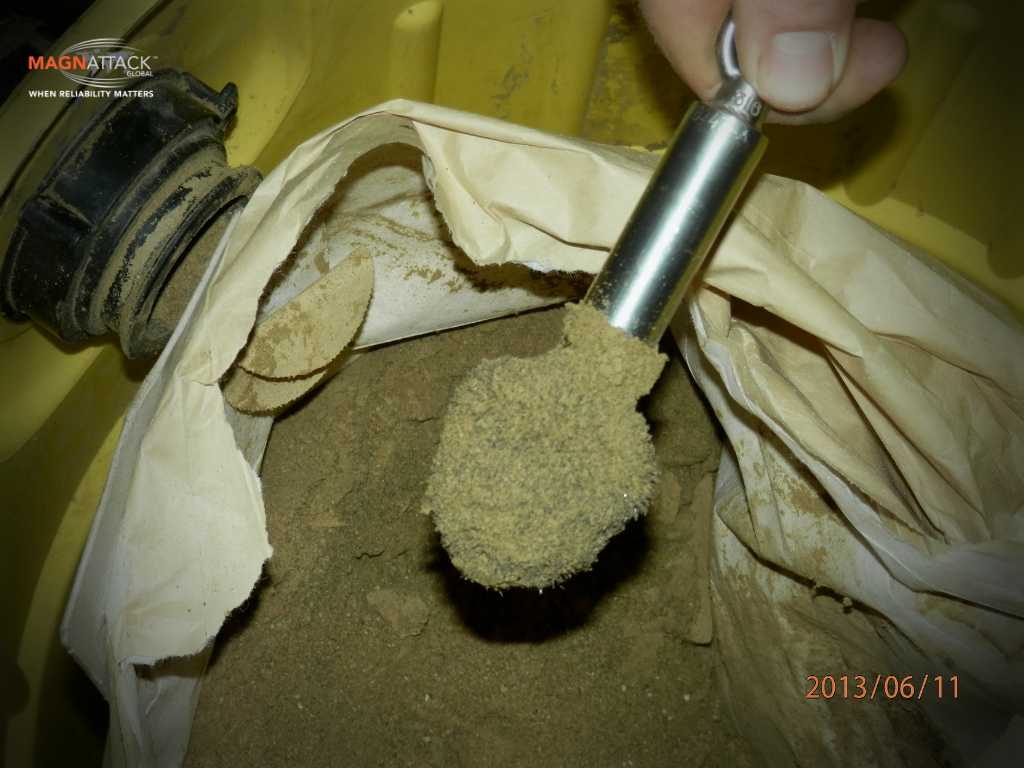
Ineffective Magnet Systems
Grate magnets, both manual and self-clean designs, are one of the most popular magnet systems for dry product lines – and for good reason. If engineered correctly, grate magnets can provide the metal fragment control you need to improve product value…but on the flip side, inefficient and poorly-designed systems can have a detrimental effect.
Some problems associated with ineffective magnet systems:
- Obstruction to product flow and product stream blockage
- Jamming and other cleaning difficulties
- Stainless-steel magnet sleeves
- Leakage of product
Ensuring that you achieve adequate product coverage without obstructing product flow is essential to achieving successful magnetic foreign material removal. There are several factors that will contribute to blockages such as substrate levels of water, fat, minerals, the range of temperature, and level of humidity.
A magnet that cannot be thoroughly cleaned will also cause obstruction to the product flow and lead to other issues such as jamming, abrasion on moving parts, and eventual failure. If not resolved, the consequences of obstruction to product flow will lead to risk of recontamination, equipment damage, or operators bypassing/isolating magnets to solve throughput issues.
Conventional magnet designs often consist of stainless-steel sleeves on the outside of magnet bars or a cleaning method that involves pulling a bank (multiple) of magnet bars through a common wiper seal. Both these methods can cause serious mechanical issues due to the nature of the rendered product, causing sticking and binding of the cleaning mechanism, which can lead to the magnet not cleaning properly and becoming a source for metal hazards itself!
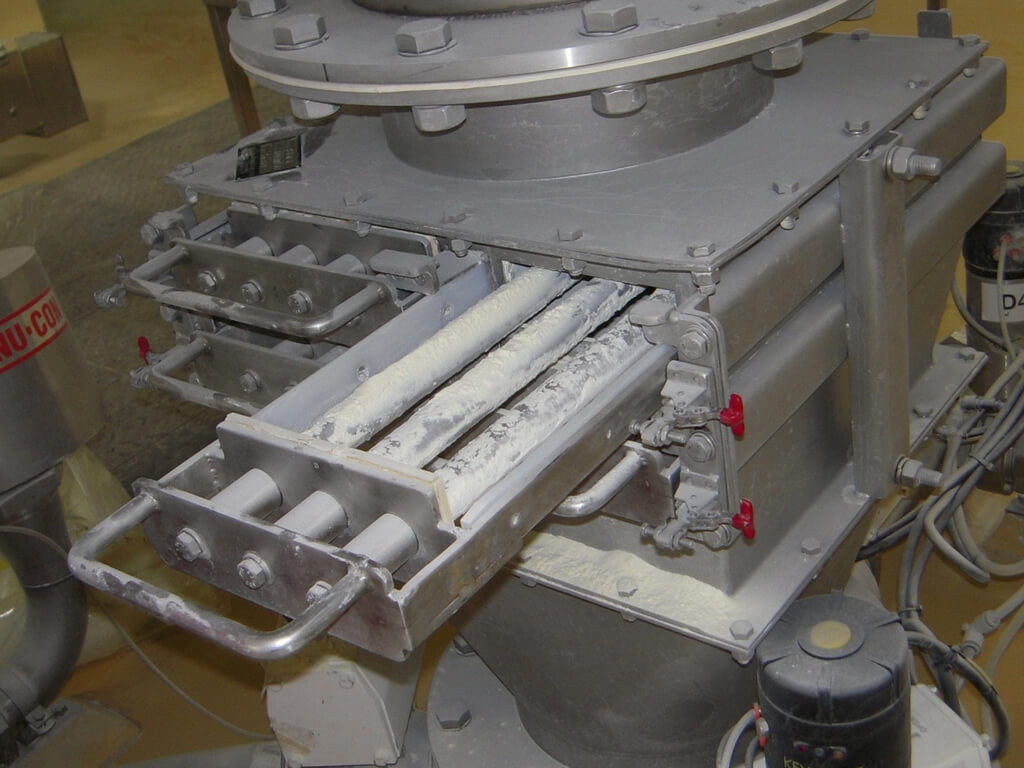
It is important that the magnetic separator is configured to mitigate these challenges and has a sequence of cleaning that ensures a clean magnet is presented to the product stream for efficient metal fragment separation.
Mag-Ram Technology Overcomes These Issues & Improves Product Value.
Engineered to overcome both these issues, the Mag-Ram Automatic Self-Cleaning Separator has been instrumental in improving meal quality for numerous Australian & New Zealand renderers and is now available to the North American market. This success is due to the advanced design of the system.
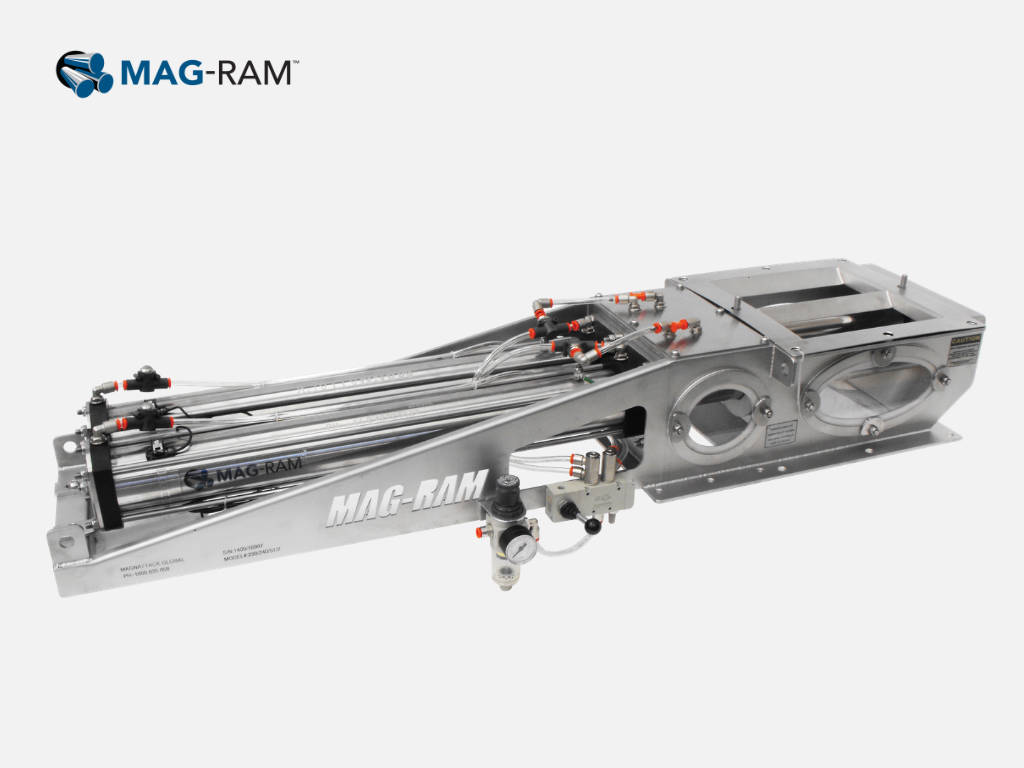
The Mag-Ram is a robust and versatile self-cleaning grate magnet which can clean before, during, and after production runs. Each Ram (or magnet bar) is the Ram of a pneumatic cylinder. Although the system can be configured to clean all Rams simultaneously, one of its many advantages for the rendering industry is its ability to clean one Ram at a time, at periodic intervals. This ensures that clean magnets are continuously being presented to the product flow and production does not need to stop for cleaning schedules. This is a huge advancement in improving metal fragment control, compared to magnet technology which relies on manual cleaning and risks magnets overloading and ‘shorting out’ if cleaning schedules are missed.
MBL Proteins, an Australian establishment, greatly increased their meat meal value and customer satisfaction after replacing their existing magnets with Mag-Ram Separators. In the comparison tests between their existing magnets and the Mag-Rams, the client found that the Mag-Ram provided a much leaner contaminant sample and demonstrated that it would give them tighter metal fragment control.
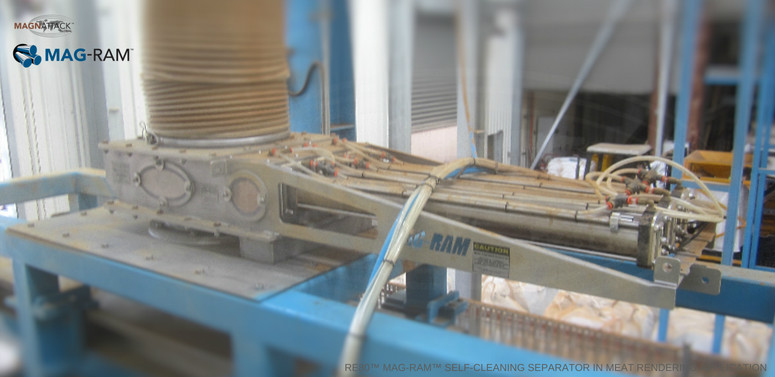
Further to the above results, the following unique Mag-Ram features have proven beneficial in rendering installs:
- 13-degree twist – each magnet Ram conducts a 13-degree twist when it is retracted for cleaning. This patented feature not only helps provide maximum longevity through wear equalization of all moving parts and seals, but also helps tip the pyramid of product off the top of the Ram, which contributes to a leaner contamination sample. In addition, this feature helps to prevent product build-up and consequent blockage.
- Dura-Slik™ Surfacing Technology – varied moisture levels, temperature, fat content, humidity, ash levels, and other factors impact the flow of rendered product. Dura-Slik Technology has anti-stick properties which keep residue build-up on the magnets to an absolute minimum, in comparison to polished or mill SS finish. This also helps to reduce abrasion to the magnets, reduce risk of demagnetization, and …tie it back to product purity.
- Customizable cleaning-cycles – The unit can be controlled with either a PLC or stand-alone controls, to whatever parameters are needed, based on the degree or level of contamination/metal hazards in the product.
- Efficient and effective cleaning – As previously mentioned, each magnet is the Ram of a pneumatic cylinder. This means no ‘walking’ or ‘jamming’ when attempting to clean multiple bars simultaneously, as is the case with conventional designs attempting to coordinate two air cylinders to pull a bank of magnet bars through a common wiper. The conventional cleaning method has always been troublesome and difficult to achieve success. The Mag-Ram™ design, however, permits the use of tight wiper seals which ensures the greatest versatility of control and highly efficient magnet cleaning is achieved. The Mag-Ram is also extremely hygienic, due to the absence of stainless-steel sleeves which inherently build up with unclean product residual.
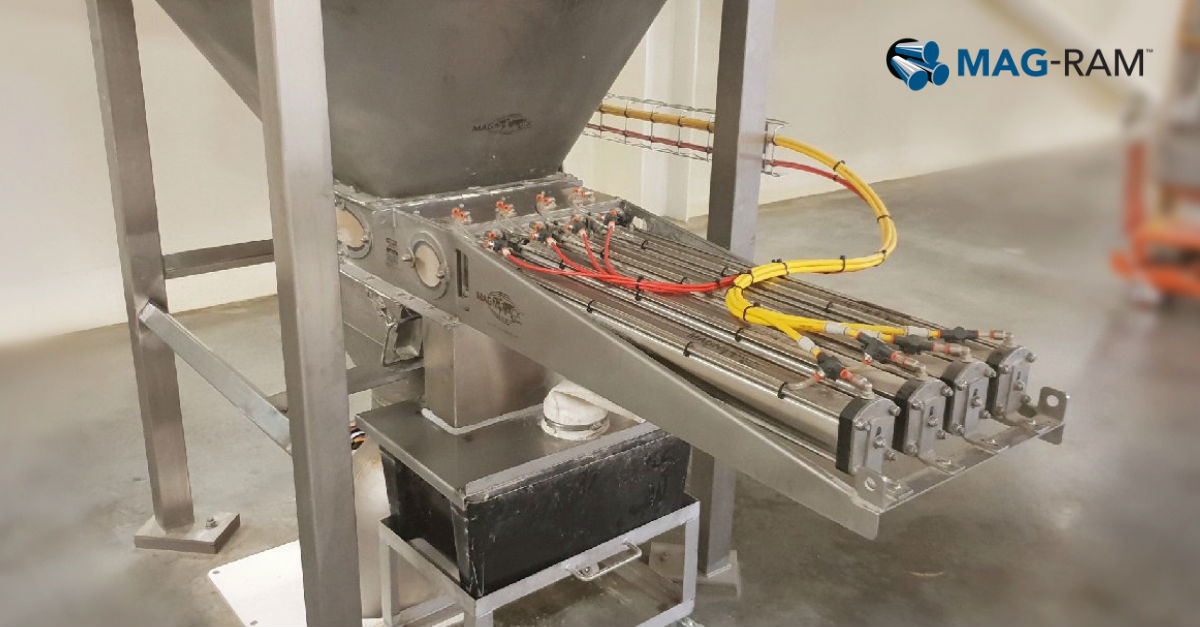
Another client, Wade Phillips of JBS, comments that “Not only does it save time and labor cleaning the magnet, it is our insurance policy that the product will support our reputation and meet the customer’s expectation, especially overseas.”
The Importance of Location
Not assessing the process properly and installing magnets at incorrect locations can leave your product at risk and impact product purity and value.
Effective magnetic separators should be installed:
- At bulk intakes
- Raw materials following initial screening
- Prior to metal detectors (reduce rejection rate)
- Prior to critical processing equipment (reduce damage and downtime for repair)
- Bulk out loading locations and prior to packing
In terms of product purity, the most crucial location for metal fragment control is at bulk out loading and packing locations. This is usually the last chance to remove any foreign metal that may impact your product value. It is vital that the magnetic separator in this location is effective and able to operate effectively and efficiently.
Plant Risk Assessments, carried out by trained and qualified metal fragment control technicians, can be invaluable in determining areas of risk in your process lines and deciding where magnets should be installed to provide maximum risk reduction.
Conclusion
In terms of increasing value and profit, it is in the renderers best interests to produce a higher quality product, and this involves decreasing the level of metal contamination. A purer, less-contaminated meat meal is more attractive to pet food manufacturers, who will pay a higher price. Low-quality product is often restricted to stock feed and may produce lower value and lower profit.
The CEO of a large Australian rendering company believes that “The Mag-Ram was instrumental in securing a long-term client that was very close to dropping us due to a number of contamination issues. Once we proved the level of control that the Mag-Ram could offer, we then become their most valuable supplier.”
By overcoming issues presented by inefficient and inadequate magnetic separators, and providing maximum foreign metal fragment control, the Mag-Ram Self Cleaning Separator has proven to be a valuable and worthwhile addition to several rendering plants around the globe.
Want to reduce risks and improve your product security? Contact a Magnattack technician today.
The Mag-Ram is widely patented in Australia, New Zealand, North America, and Europe.