Achieving Effective Magnetic Separation Without Affecting Line Pressure
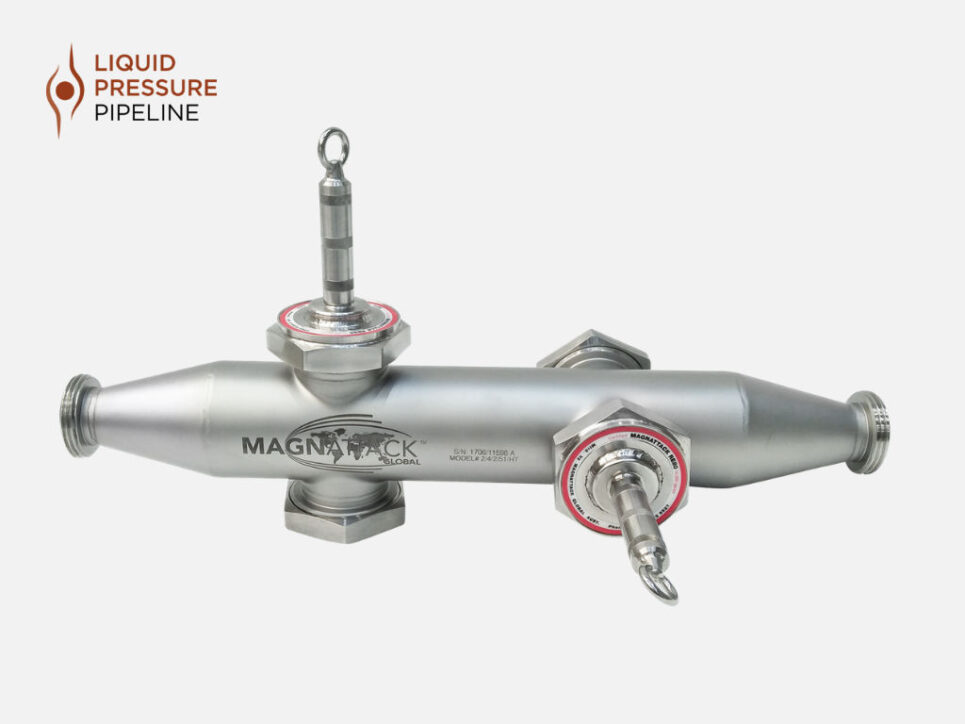
In accordance with HACCP International Food Safety Standard 0909MAGSEP 1-2010 and our own criteria, Magnattack® RE80® Magnetic Separators are designed to achieve maximum product stream coverage. This often involves large diameter, high-strength magnet probes inserted into a pipeline.
Understandably, sometimes our customers raise concern about the changes to line pressure that may result. This is especially so in liquid pipelines.
An increase in line pressure can have several undesirable consequences, including:
❌ Change in product characteristics, including particle sizes and viscosity
❌ Leaks, blockages, build-up
❌ Damage to plant and equipment, and possible danger to operators.
However, this is one of the challenges associated with inadequate magnets that our technicians have accounted for when designing Magnattack® separators. Here we discuss two key design features that help our customers maintain line pressure and decrease the risks listed above.
Larger Diameter Housings
A calculated increase in body sizing is one design feature of our magnets that contributes to keeping line pressure consistent. You can see this in the below images of the RE80®HT Liquid Pressure Pipeline Separator and RE80®HT Emulsion & Slurry Pipeline Separator.
In each example, the diameter of the housing where the probes are situated is larger than the diameter closer to the inlet/outlet fittings, however at the same time, maintaining consistent open area to avoid pressure variations.
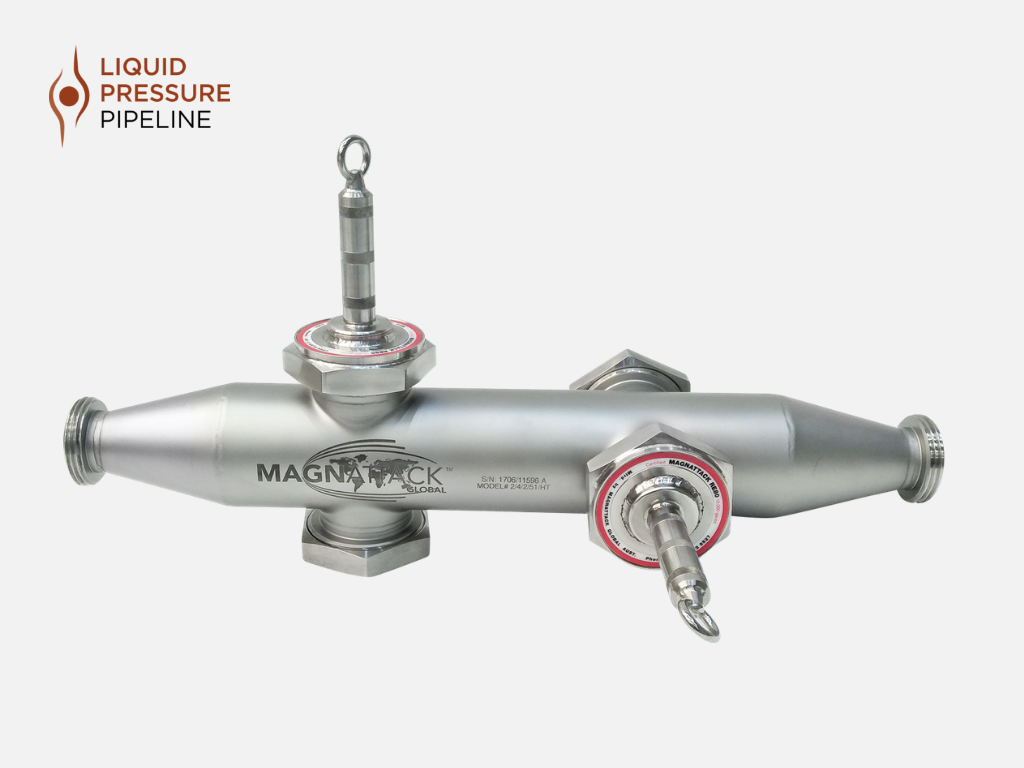
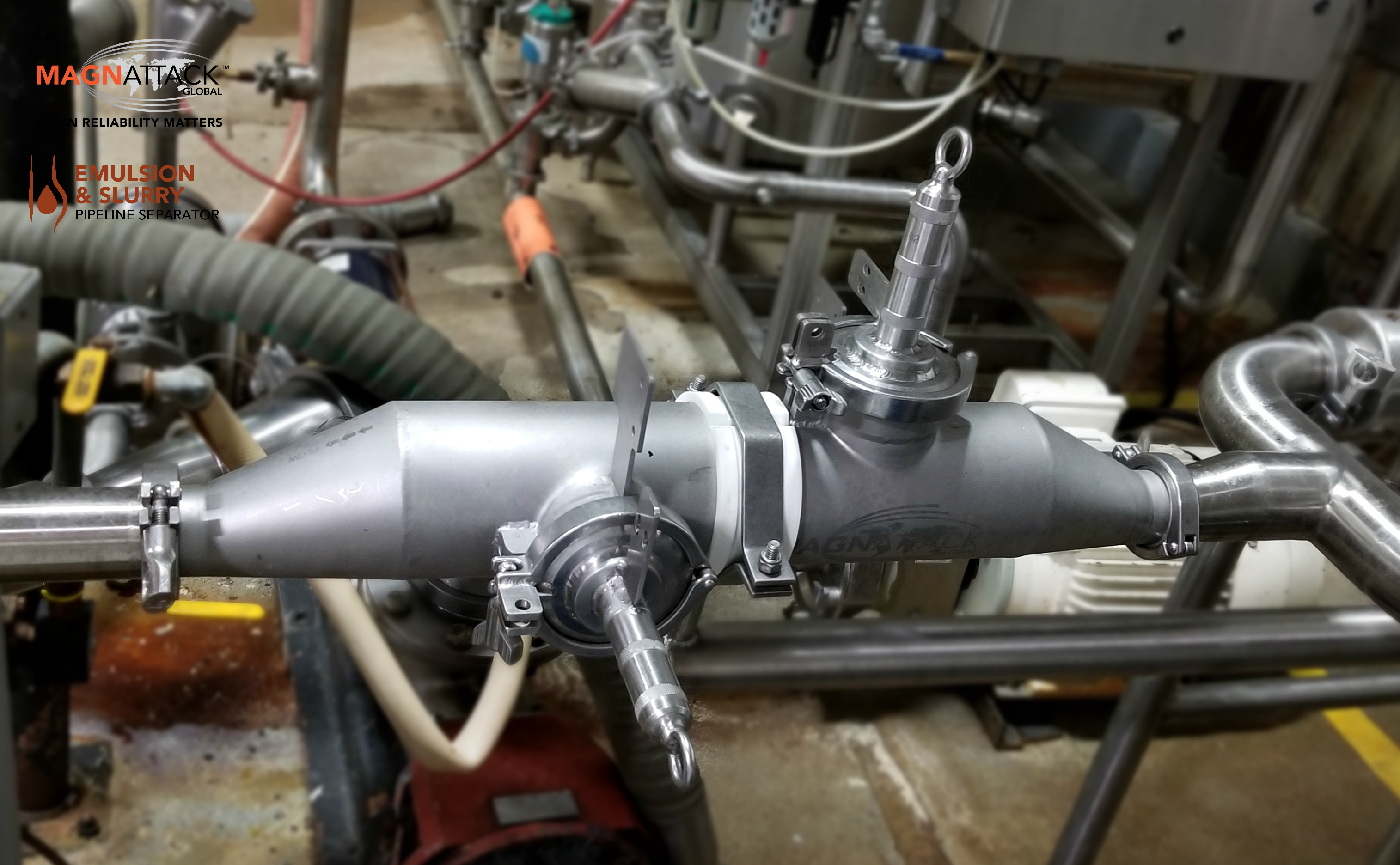
Acutex Probe Magnets
Specially designed Acutex™ Probe Magnets consist of a pointed/tapered end that faces the oncoming product. This efficiently ‘splits’ the product stream in half so it can flow smoothly around the outside of the probe. Metal contaminants can be pushed to the back of the specially shaped magnet bar, minimizing turbulence, and in turn, reducing the risk of losing metal fragments back into the product stream.
The Acutex™ Probe and open-area matrix is formulated for each product, dependent on specific flow properties. This is effective in preventing pressure or impact that could otherwise cause changes in product characteristics.
Pressure and product build-up increase the likelihood of re-contaminating the product stream with collected fragments, so this distinctive shape of the Acutex™ is also very important in reducing re-contamination risks.

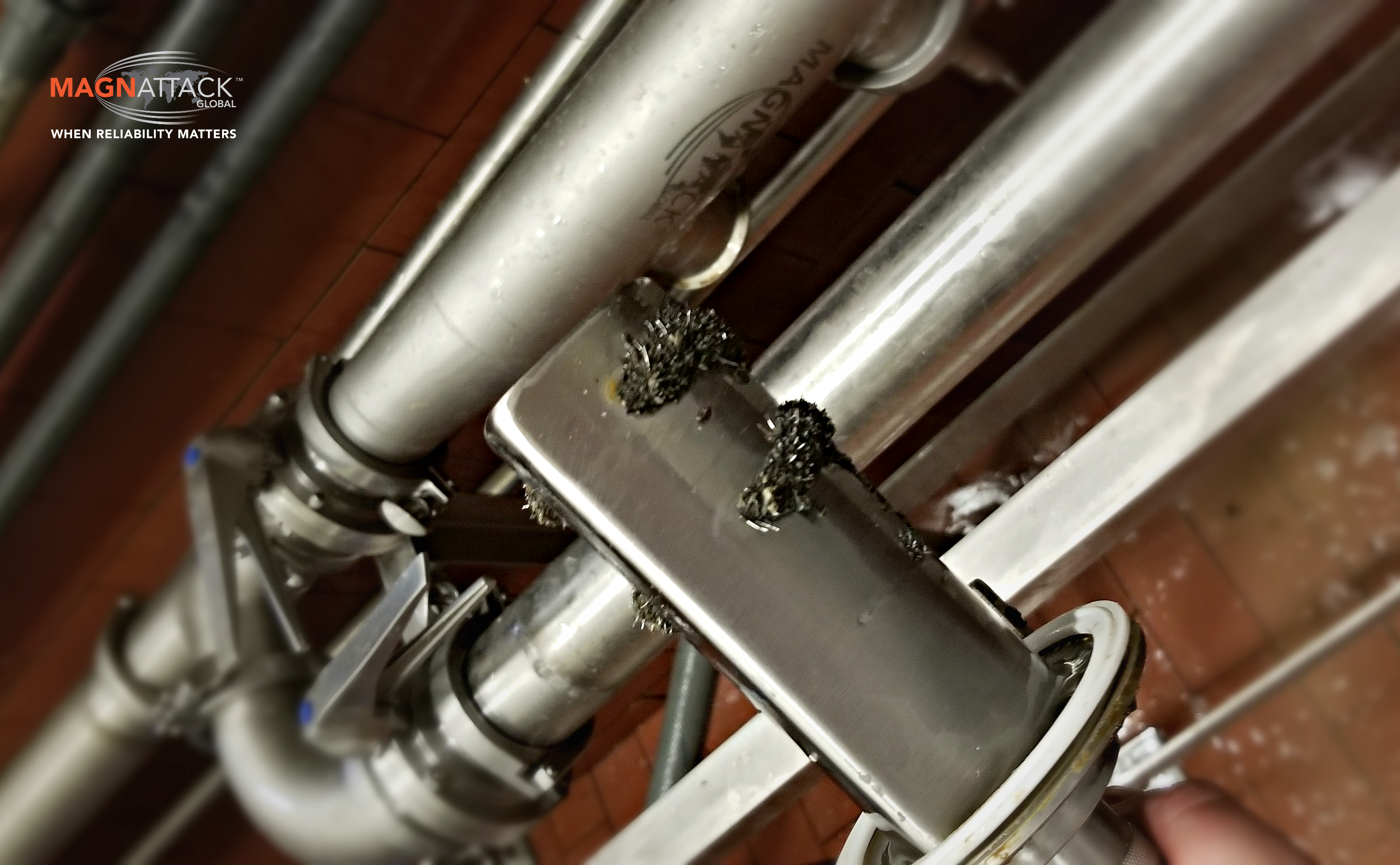
Looking for more effective magnets?
The difference between an effective magnet and an ineffective magnet is often the impact it has on line pressure…which is why it is so important that magnet manufacturers understand this and design their magnets to reduce this risk.
In summary:
❌ An ineffective magnet can cause line pressure, product build-up and flow issues, and distort important product characteristics. It can also increase the risk of re-contamination.
✔️An effective magnet will be designed to have minimal to ZERO impact on pressure or product flow, will maintain product quality, and ensure efficient separation of metal contaminants without leaks or blockages!
Contact our experienced team today.
We have 50 years of experience in metal fragment control solutions for the food industry. Our qualified technicians will consider your individual and unique applications to help you select magnetic separators that benefit you and your company!