Magnattack® Spherical Magnets now also available in dairy-grade
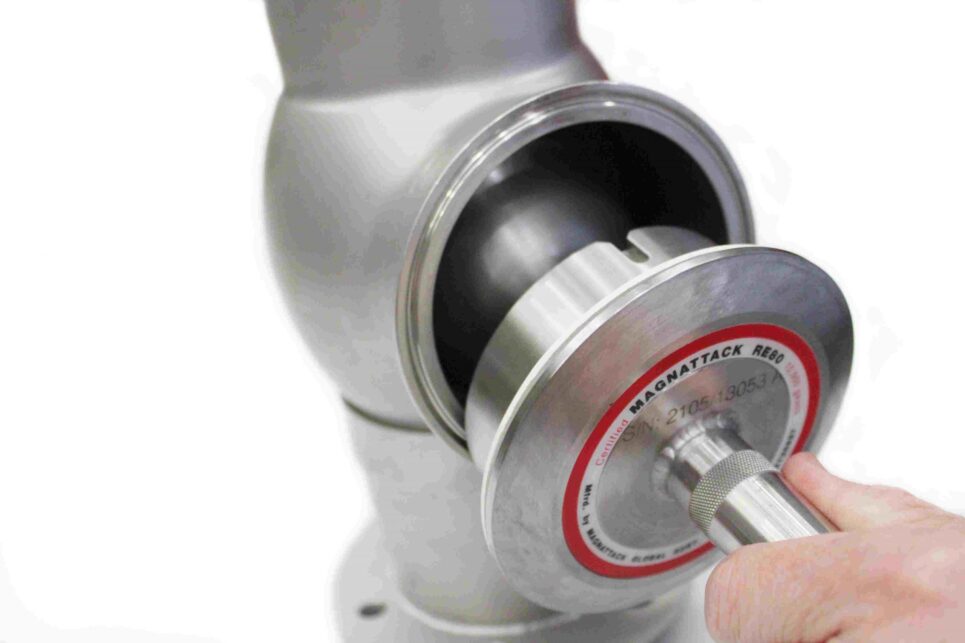
One of our most powerful magnet designs is now also available in a dairy-grade option: the Spherical Pneumatic Transfer Magnet.
This high-intensity magnetic separator has been a major success in various industries, ranging from meat rendering to bakeries, and is now also becoming rapidly popular in the dairy industry. Designed for high-velocity pneumatic transfers, these magnets are equipped to handle the tough, dry ingredient applications. The Spherical is now available fully welded, creating a hygienic one-piece design for sanitary applications.
The Spherical Pneumatic Magnet was originally designed for an Australian mill, where blockage issues were a common problem. Due to the challenging nature of a pneumatic blowline, the client needed a magnetic separator which would last and have the ability to collect and retain the magnetic fragments from the product.
The Spherical Magnet performed exceptionally well in the challenging application.
Watch our technician, Calvin, showing this 20+ year old Spherical Magnet which is still going strong! Over 20 years later, this magnet is still over 10,000 gauss, and on supply, the Spherical Magnets can be up to 15,000 gauss!
Key Benefits and Features
- Effective separation of foreign metal contamination in high-velocity powder applications without experiencing bulk density changes and pressure loss
- Aerodynamic design prevents blockage of product and minimizes product particle breakdown.
- Internals of housing are self-cleaning due to the aerodynamic design with no internal ledges
- Provides a very reliable indication and protection against incoming metal contamination
- Optimum product stream coverage enabling highly efficient separation of weak to highly magnetic fragments
- Reduced risk of re-contamination. Due to the engineered spherical shape of the magnet, the captured material will tend to move around, by the flow of the product, to accumulate in the low-velocity region behind or around the back of the Sphere. This will increase the capability of the magnet to retain metal fragments and minimize cleaning frequency. In comparison, Bullet Magnets have a flat base or flat raised poles which often do not hold tightly enough to weakly magnetic fragments, therefore risk being dislodged and re-entering the product flow
- Dura-Slik® Abrasion Reduction Technology – this is an FDA-approved anti-stick surface treatment which helps reduce surface tension with sticky powders. It also provides barrier protection against galvanic surface reaction in more corrosive environments
- RE80® Magnet Technology – only the highest specification raw materials are used, and all components are manufactured to the highest tolerances to resist the onset of demagnetization
- 11-15,000 gauss strength available depending on design and specification. (In comparison, most bullet and plate systems don’t exceed 7-8,000 gauss)
Where to install Spherical Magnets
- Incoming ingredients
- Prior to metal detectors
- Prior to critical processing equipment
- Prior to bagging operations, bulk out loading, or direct filling of trucks (e.g. flour trucks)
- Dilute/lean and dense phase applications of 3″ – 8″ (75mm – 200mm) in size.
- Suitable for high velocity and large volume vertical installations in blow, vacuum, gravity, & pneumatic transfer lines