MBL Proteins Improves Meat Meal Value with the Mag-Ram Self Cleaning Separator
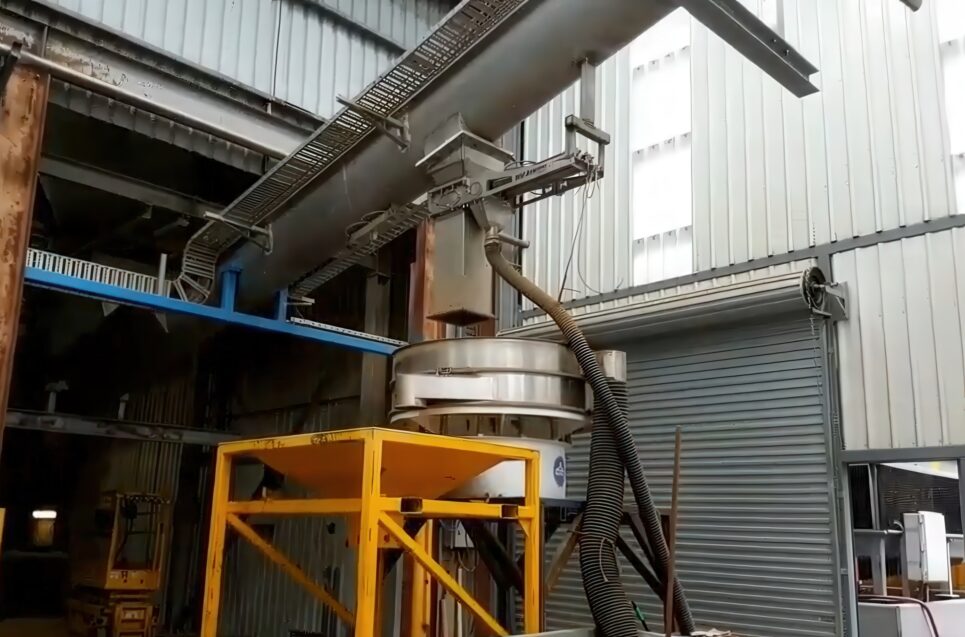
To reduce metal fragment contamination complaints, MBL Proteins, a respected Australian meat rendering company, found a way to increase meat meal value and customer satisfaction by replacing their magnets with a number of strategically placed RE80 Mag-Ram Automatic Self-Cleaning Magnetic Separators.
Exploring Their Options
MBL Proteins, like most meat renderers, already had self-cleaning magnetic separators installed in their meat and bone meal process, however, it was becoming apparent that they needed to enhance their level of foreign object metal fragment control in several of their finished products.
The aim of the project was to produce a higher quality product and increase customer confidence.
Although they could have simply installed additional magnets to provide another level of protection, it was necessary to determine whether this would be most effective or whether they should replace them with completely new systems. MBL needed to ensure that their foreign object metal fragment controls were efficient, fit for purpose, and cost-effective, and so they saw the need to conduct controlled testing in the rendering environment between different types of self-cleaning magnets. They were intending to find the comparison benefits between 10,000 gauss strength bar magnets and also including deep field drum style magnets.
Magnattack Global was contacted by Gary Deutrom to provide equipment as part of this testing where they could accurately evaluate the performance of the Mag-Ram™ vs the other self-cleaning alternative.
Satisfying Results
In comparison to the Mag-Ram™ system, other self-cleaning magnets were yielding an unacceptable level of product carry over into the contamination side of the chamber. There was also evidence of a much higher percentage of metal contamination still escaping the magnet, due to the challenges that a typical meat meal process presents.
The Mag-Ram™ was well engineered for the rendering environment providing a much leaner contaminant sample. The Mag-Ram™ demonstrated that it would give them greater control over foreign metal, less product wastage, increased product quality and value, and lead to improved customer satisfaction.
This was extremely important to Site Manager Gary Deutrom, who says that “when you are producing a premium product for export markets, you can’t afford to be scalping good product away from an inefficient magnet”.
The features that are truly unique to the Mag-Ram™ and highlighted in this trial as follows:
Built in wear equalization – Each time the magnet Ram retracts for cleaning the Ram returns in a different position due to the activation of a special equalization mechanism deep within the magnetic assembly. This patented feature not only helps provide maximum longevity through wear equalization on the magnet and moving parts and seals, but also helps dislodge the pyramid of product on the top of the Ram, which contributes to a leaner contamination sample.
Dura-Slik Surfacing treatment – Varied moisture levels, temperature, fat content, humidity, ash levels, and other factors of MBM processing can hinder the flow. Magnattack’s Dura-Slik Surfacing treatment has anti-stick properties which minimize residue build-up, in comparison to polished or mill SS finish. This also helps to reduce abrasion to the magnets.
Exhaust Air Clean – Any additional clean product that may be still be seated on the magnets when they are retracted into the contamination chamber for cleaning will likely be directed away by a gentle calibrated air stream (whilst leaving the magnetic contaminants on the magnet). This helps to further minimize the total loss or wasted clean product.
Cleaning Programme – The frequency of the cleaning cycle can be adjusted for optimum timing depending on the demand for each application.Such as continual cleaning or coinciding with screw fed application.
The results from this testing assured MBL that they were making an informed decision for the investment of future magnetic separation equipment. Since implementing the latest Mag-Ram™ separator systems, it was quickly recognized and appreciated by the client of MBL due to the noticeable improvement.
CEO of MBL Proteins, Warren McLean, tells Magnattack that the Mag-Ram was instrumental in satisfying their customer’s expectation – “there are many hazards that can find a way into MBM production. Once we can demonstrate to our customer that were are doing everything we responsibly can to control that which we can control, the rewards are being able to offer than higher value product, and that is valued by the customer”.
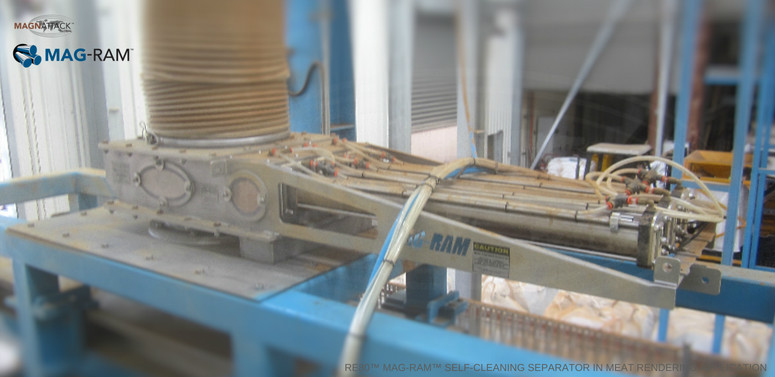
Justifying The Cost
On justifying the cost, McLean says “the Mag-Ram is not an asset that increases the output capacity of the plant, so it was important to look deeper into the justification to manage the metal contamination risks. In this, we found that the Mag-Ram systems have become like our insurance policy to our customer”.
In terms of increasing value and impacting the bottom line, it is in the renderers best interests to produce a high purity product, and this includes reduction of metal contamination. A high purity meat meal is more attractive to a broader range of users for optimum return. A lower-quality product is often restricted to stock feed grade product.
By overcoming issues presented by inefficient and inadequate magnetic separators, and providing maximum foreign metal fragment control, the Mag-Ram Self Cleaning Separator has proven to be a valuable and worthwhile addition to several rendering plants around the world.
The Mag-Ram is widely patented in Australia, New Zealand, North America, and Europe.