Metal Fragment Control For Food Safety, Product Security, And Brand Protection
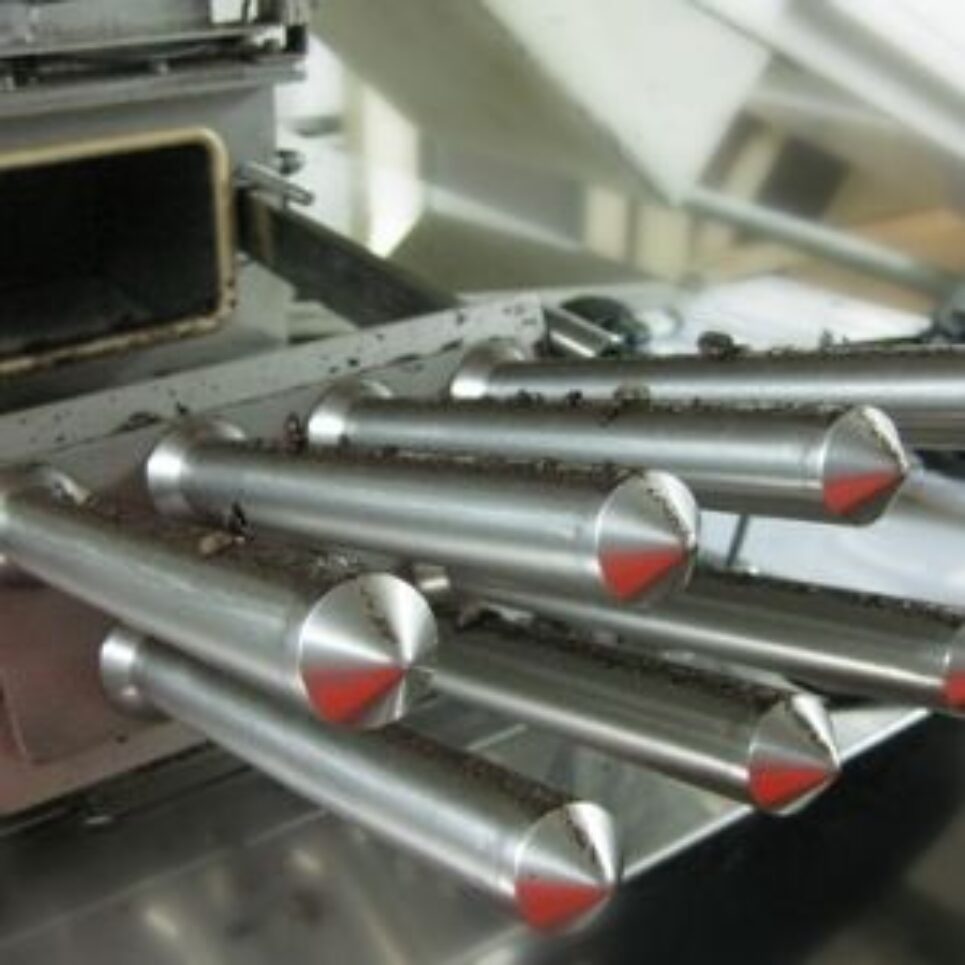
Adequate procedures, cutting-edge magnetic separation equipment, and metal detectors are essential for the control of weakly magnetic fragments to maintain food safety initiatives, improve product purity, and protect brands.
Combined with a greater focus on hygiene, operator safety, and lean manufacturing practices, this food safety initiative has led to the development of a combination of both ultra-high intensity magnet systems and highly sensitive metal detectors/x-ray units. This allows food processing companies to successfully control foreign matter detection.
Most stainless steel fragments and wires smaller than 0.19″ / 3mm in size are usually work hardened (meaning they are weakly magnetic) and because of their small size, often go undetected by metal detectors. Modern ultra-high intensity >10,000 gauss certified magnets fill this gap and allow for such foreign matter, including magnetic stone and wear iron, to be extracted magnetically. This further reduces the serious risk of contamination, product recall, and brand name damage.
With an efficient design and high-end detail during the manufacturing process, Magnattack Global specialize in providing ultra-high intensity RE80™ >10,000 gauss magnet systems of both manual and self-cleaning designs to ensure fine ferrous metal and fine magnetic fragments are extracted and retained in critical applications both prior to processing and at final packing of products.
Further advantages of RE80™ magnet systems include the overall reduction in nuisance metal detector trips prior to packing, as these upstream >10,000 gauss magnet systems extract most of the foreign ferrous matter prior to the detection process – thus reducing the time and effort involved in locating contaminated product within bulk bags and bins. Damage to expensive process machinery is also reduced or eliminated as RE80™ power easily grabs and retains tramp iron.
This means the worry is taken out of metal fragment contamination control, leaving food manufacturers free to concentrate on other vital food safety controls.
The Magnattack team have over 45 years of experience working closely with a worldwide base of clients and food industry engineers to ensure magnet systems are adequately designed and manufactured to current HACCP International and USDA magnet standards. Magnattack continue to provide a positive contribution to product security and food safety through research and development programs and guarantee individual attention to customer specific applications with the highest levels of before and after-sales service.
Magnattack Global have a strong association with a separate company, AMR Consulting, who conduct and coordinate magnet validation services worldwide in accordance with current HACCP standards and procedures. Rather than just receiving a magnet validation from a magnet supplier, a more independent type of report is available, using the expertise of experienced food technologists. This ensures that the information in the report received is not only is accurate but also completely conforms to magnet requirements detailed in the current HACCP International Food Safety Std 0909MAGSEP 1-2010.
To ensure you are properly covered by separation systems, reference should be made to the current metal detector and magnet standards. Magnets should conform to current HACCP International standards with the additional importance of specifying factors beyond magnet strength – such as product stream coverage, retention efficiency and hygiene and construction requirements.
For foreign matter applications of current concern, planning in of new projects or to receive your guide for effective magnet installations, please contact us.