Reducing Metal Fragments From Your Baking Ingredients
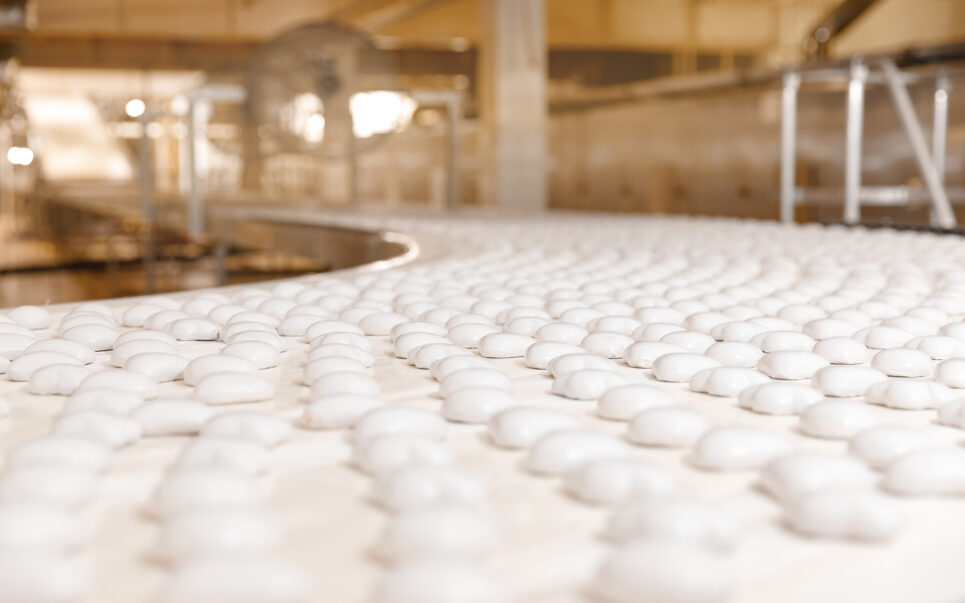
Explore the essential role of magnetic separation in ensuring the purity and safety of baking ingredient production. Learn about the risks of metal contamination, how to implement magnetic defenses, and choose the right magnet expert for reducing contaminantion in ingredient processes.
Understanding Magnetic Separation
Magnetic separation is a process that uses magnets to remove magnetic materials from a mixture. It exploits the material’s magnetic properties, separating magnetic particles from non-magnetic ones. Due to its efficiency and simplicity, this method is used in various industries, including mining, recycling, and food production.
For instance, magnetic separation plays a crucial role in the manufacturing process of food ingredients such as flour and semolina. Here, it helps eliminate foreign metals, ensuring higher purity of the baking ingredients.
The Potential Harm of Metal Contamination in Baking Ingredients
Metal contamination in baking ingredients can lead to serious health risks, from minor digestive issues to severe injuries or poisoning. Foreign metals can be introduced during the growing, harvesting, transportation, or milling processes. Consuming baking ingredients contaminated with metal fragments might pose a risk to health of consumers and have a negative impact on the producers of those food products, including product recalls, financial and legal issues, and brand reputation damage.
How Metal Contaminants Enter the Baking Ingredient Production Process
Metal contaminants can enter the ingredient production process in numerous ways. During harvesting, metal fragments from machinery or tools can be mixed with the grain. Similarly, during milling, parts of the mill can wear down, adding metal particles to dry baking ingredients. Effective magnet separation systems are crucial to catch these contaminants.
The Impact on Food Safety and Quality
The presence of metal in baking ingredients can significantly impact food safety and quality. Regulatory agencies have strict guidelines for allowable metal levels, and exceeding these can lead to recalls, financial loss, and damage to a brand’s reputation. Thus, maintaining efficient magnetic separation systems is not just a matter of quality but a necessity for safety.
Utilizing Magnetic Separation in Baking Ingredient Production
Magnetic separation begins with magnet systems installed at various strategic locations along the production line in the dry ingredient milling industry. Typically, separators are placed at product intakes and first break, mid-process, at final packing and bulk outloading, and at gravity bulk outloading locations. This staged approach ensures the maximum removal of metallic contaminants.
Bar Magnets
Bar magnets are fundamental tools in various industries due to their simplicity and practical design. These magnets are designed to remove magnetic materials from processing lines, and are widely used in food processing, pharmaceuticals, and recycling industries. Positioned at critical points where contamination is most likely to occur, such as at the beginning or end of a production line, these magnets serve as a primary line of defense, ensuring the purity and safety of the products. It is simple yet effective and often used at critical points to catch metal fragments.
Drum Magnets
Drum magnets are used mostly in dry free flowing large tonnage applications, especially in sectors dealing with bulk grain flows, such as agriculture, milling, and food processing. These magnetic separators consist of a rotating magnetic drum. Often Installed above conveyor belts and storage hoppers or on large volume intakes areas, drum magnets attract and retain ferrous contaminants, pulling them away from the grain flow. Their effectiveness in continuous operations makes them indispensable for maintaining the quality and safety of grain products, protecting downstream equipment from potential damage caused by large metal pieces.
Grate Magnets
Grate Magnets are applicable to almost all of the above-mentioned locations and can be very effective in removing metal contamination from the product – if an adequate design is selected! Due to the abrasive nature of milling products, magnets can suffer rapid abrasive wear, but the development of the Magnattack® Mag-Ram® Self-Cleaning Separator (link) has removed the need for many other magnet designs, such as plate, hump and drum magnets.
Designed for low-headroom applications and build-in contingencies for anti-abrasion, as well as an ever-changing contact point on the bars, the Mag-Ram® has proven a fantastic and economical choice for many milling applications.
The Magnattack® Rapidclean® Drawer Magnet is another excellent choice for milling applications, with the anti-abrasion Dura-Slik® option and design made for easy cleaning with reduced re-contamination risks. (link)
Magnetic Humps
Magnetic humps are specially designed for gravity flow systems where material passes through chutes or vertical drops. These devices consist of two plate magnets mounted at an angle, forming a “hump” through which the material is directed to flow. As the product passes between these magnetically charged plates, any ferrous contaminants are attracted and held against the magnets’ surfaces, effectively removing them from the flow. This solution is designed for industries where material handling involves vertical transitions, and the natural force of gravity can be utilized to enhance separation efficiency and used when material falls through chutes, taking advantage of gravity to remove metal particles.
Plate Magnets
Plate magnets are versatile magnetic separators commonly installed in ducts, chutes, or under conveyor belts. Their flat design allows them to be placed directly in the path of material flow, creating a magnetic field across the entirety of the flow area. As materials pass over or under these magnets, ferrous particles are attracted and held firmly to the magnetic surface, preventing them from continuing downstream. This magnetic separation method is particularly effective in industries where fine, powdered, or granular materials are processed, ensuring product purity and protecting delicate machinery from metal contamination. Commonly found in ducts and chutes, these create a magnetic field across the flow to catch metallic particles and potentially damaging, highly magnetic tramp metal pieces.
Pneumatic Transfer Magnets
Pneumatic Transfer Magnets, such as the Spherical Pneumatic Transfer Magnet, can be well-suited for mid-process applications and low-abrasion transfers of wheat/rice flour, semolina, bran, and soft grains such as barley, sesame seeds and quinoa.
Magnattack® Spherical Pneumatic Transfer Magnets are an extremely effective means of collecting fine weakly-magnetic fragments from final flour and milled products as well, and can be positioned upstream of cyclone storage hoppers or in bulk fill blowlines to tankers, etc.
The bulk of the high intensity magnetic energy that the RE80® Spherical Magnet produces, combined with the high coverage and surface area of the Spherical element, ensures that extraction of weakly-magnetic fragments in high velocity blowlines is extremely successful. Spherical style magnets boast huge surface strength giving a superior advantage to conventional inline spout and bullet type magnets to retain the metal fragments connected, out of the way of the high velocity flow of product.
Finding new solutions to your magnetic separators doesn’t have to be difficult. When it comes to hump magnets vs bullnose magnetic plates, make sure you get professional advice to ensure optimum separation is achieved!
The Effectiveness of Magnetic Separation in Reducing Metal Contamination
The effectiveness of magnetic separation in reducing metal contamination is impressive. The majority of metallic contaminants can be removed by strategically placing magnetic separators at crucial points in the production line. This significantly reduces the risk of health hazards and damage to machinery, and ensures compliance with food safety standards, thus maintaining the integrity and quality of the baking ingredients.
How to Find a Reliable Magnet Consultant and Installer
When you need a solution for your milling and bakery processes, consider all of your options for magnetic separation partners. Here are some ways to ensure a fruitful partnership with any magnet technician, and how to make the right choice for your business.
Research
When looking for a reliable magnet consultant or supplier, thorough research is essential. Start by looking into companies specializing in magnetic systems for the food industry. Check their credentials, read customer reviews, and compare their services. Look for information on their magnetic separators, especially those suitable for dry ingredient mills, and how they compare to other conventional designs.
Asking Questions
Once you’ve narrowed down your options, approach each company with a set of questions. Ask about their experience with baking ingredient mills, the effectiveness of their magnetic separators in reducing metal contamination, and how they plan to address your specific needs. Inquire about installation processes, ongoing support, and any financial benefits of integrating their system into your manufacturing process. Also, understanding what is done to reduce magnet strength loss over time, through built-in design contingencies is an important consideration when choosing a long term, effective solution.
With the right partner, you can ensure that foreign metal contamination risks in your baking ingredients are reduced, your process adequately meets food safety standards, and safeguard your product’s quality. Remember, reducing metal contamination not only protects your consumers but also preserves the integrity of your brand and your most expensive investments.
Invest in Your Business’ Quality With Advanced Magnet Separation Equipment From Magnattack Global
When you need solutions, turn to Magnattack for reducing foreign contaminants in your food products. Our line of dry separation equipment will improve quality and give you peace of mind throughout your food processing timeline. Contact us today for a consultation.