What is magnetic separation?
What are magnetic separators? Where are they used? How do they work? Why are they needed? These are questions that are commonly asked by people who are unfamiliar with the process of magnetic separation. So, we’re breaking it down.
WHAT IS A MAGNETIC SEPARATOR?
A magnetic separator is a piece of equipment that magnetically attracts and removes foreign metal pieces from other materials. They are typically installed in a line of flowing materials and can be used in conjunction with metal detectors and x-ray machines for maximum defense against contamination and damage to expensive equipment.
A magnetic separator can vary greatly in size, configuration, and how they operate, depending on the industry and product in which they are intended for. Some types of magnetic separation equipment include grate magnets, pulley magnets, inline magnets, suspension magnets, self-cleaning magnets, liquid line magnets…this list could go on and on and on.
Despite their differences, all types are created with one mission in mind: to extract unwanted metal contaminants. Having said this, there are a vast variety of different ferrous metal types that require extraction – from large tramp iron in mining situations to tiny work hardened SS fragments and metal dust in sensitive food ingredients.
WHERE ARE MAGNETIC SEPARATORS USED?
The process of magnetic separation is utilized in many industries, some of which include:
- Food and beverages,
- Pharmaceuticals,
- Recycling,
- Mining,
- Coal,
- Aggregate,
- Plastic,
- Rubber,
- Chemicals,
- Packaging, and
- Textiles.
Throughout each industry, a variety of different magnetic separators are used depending on the installation location and the product that the metal contamination is to be removed from.
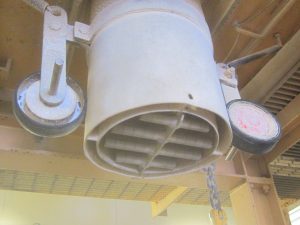
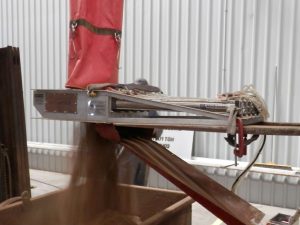
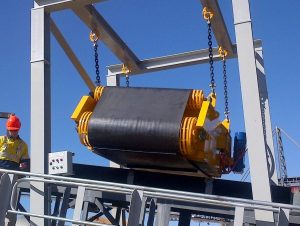
HOW DO MAGNETIC SEPARATORS WORK?
As mentioned above, different industries utilize different types of magnetic separation equipment. Because of the variables between types, there is no one set way for how all they all operate.
For example, pulley magnets are installed under a conveyor belt and retain the tramp metal contaminants until the belt reaches a point where the metal is no longer retained by the magnetic field, and so it drops off. Suspension or overbelt magnets are installed above product lines and extract the metal pieces from the product on the conveyor below. Grate and other inline magnets have direct contact with the product as it flows past, and retain the metal on the magnets until cleaned by an operator. Some magnets sit stationary and others move continuously. Some magnets require manual cleaning by an operator, others have a self-cleaning operation.
MAGNETIC SEPARATION IN THE FOOD, BEVERAGE, AND PHARMACEUTICAL INDUSTRIES.
Magnets that are used in the food, beverage, and pharmaceutical industries are typically set apart from the magnets designed for use in other industries mostly due to one factor – there is a much greater focus on hygienic and sanitary construction for magnets in food applications. In recycling or mining, for example, magnets are built to be robust and sturdy for heavy industrial use – it is not a huge concern to these industries if their magnets are not highly sanitary or if they do not adhere to food safety standards for food contact.
Magnets used in food processing should comply with stringent quality standards to ensure they are suitable for use in the industry. These can include HACCP, USDA, or other similar standards or practices set out by governing or advisory food industry organizations.
This is not to say that equipment for the food industry does not need to the sturdy, robust, and abrasion resistant – these features are still extremely important in order to maintain the strength life and effectiveness of the magnet. No application is the same – whilst there is always a focus on quality, food industry applications can differ from one another – for example, a dairy or pharmaceutical plant is more concerned about sanitary construction than a meat rendering plant, and a grain milling plant is more concerned about abrasion resistance than an infant formula plant.
MAGNET INSTALLATIONS IN THE FOOD INDUSTRY
Magnets are installed in various strategic locations throughout a food processing plant – from the moment a product is introduced to the factory, during processing, and throughout the entire process line including packing. Some of these locations include:
- Blowlines and vacuum lines – lean/dilute phase
- Gravity lines
- Pump lines
- Liquid lines
- Hopper discharges
- Hopper inlets
- Ingredient intakes
- Packing lines
- Bulk outload and discharges.
TYPICAL APPLICATIONS IN THE FOOD/BEVERAGE INDUSTRY INCLUDE:
- Flour, maize, and rice milling
- Meat rendering and bone meal
- Pet food and stockfeed
- Dairy
- Sensitive powders
- Pharmaceuticals
- Seeds and grains
- Liquids, including chocolate
- Baking ingredients and applications
- Snacks and confectionary
- Wine
- Breweries
- Spices and condiments
- Fruits and vegetables.
Magnattack Global focuses solely on the food, beverage, and pharmaceutical industries. This specialized focus ensures that we are able to provide a current, relevant, and knowledgeable source for the food industry to rely on in regards to metal fragment controls and magnetic separation equipment solutions.
*Disclaimer: This information is provided without prejudice and is intended to assist in education regarding developments in magnetic separation technology. Magnattack Global blog posts do not intend to undermine any product, person, manufacturer, or company, but rather intend to provide experienced opinions for assistance to the industry that Magnattack Global associates with. Please refer to Magnattack Global Terms of Use.