Snacks, Confectionery & Chocolate
The snacks and confectionery industry faces significant metal contamination risks from equipment wear and incoming raw materials, particularly in ingredients like salt, sugar, and gluten. To mitigate these risks, magnetic separators should be strategically installed at critical points in the production process, including ingredient intake areas, above bulk discharge points, upstream of powder sprinkles, as well as at post minor ingredient intakes, and at ingredient bag dump areas. Proper placement of magnets ensures effective contamination control before final products are packed, complementing downstream metal detection systems and safeguarding product quality and safety.
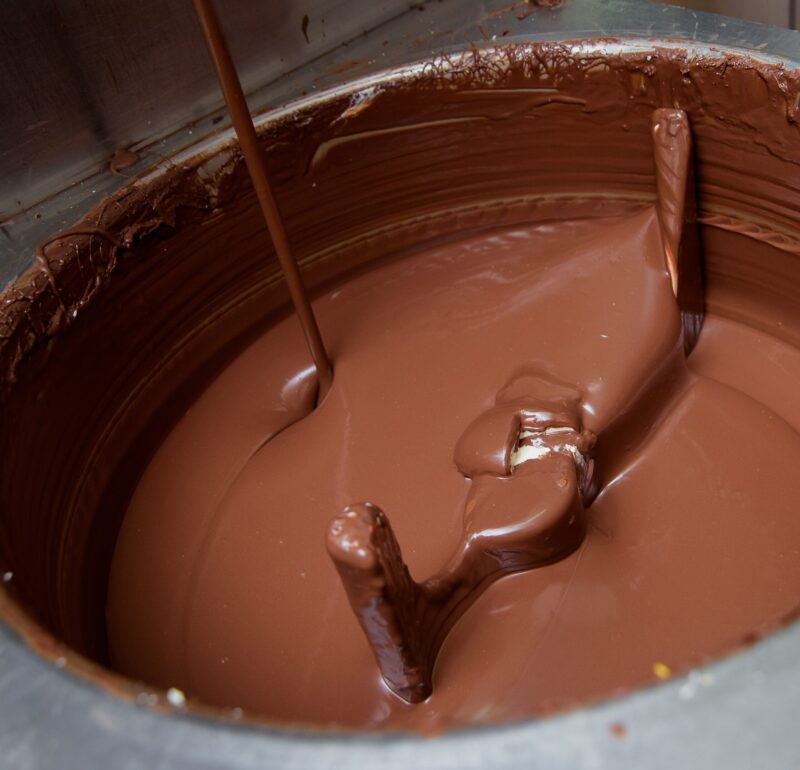
Snack Smarter: Safeguard Quality with Advanced Metal Contamination Control
The snacks and confectionery industry is highly susceptible to metal fragment contamination, stemming from equipment wear (such as chocolate conches) and impurities in raw materials. Ingredients like salt, sugar, and gluten are particularly likely to contain small metal particles, underscoring the importance of effective contamination control. Magnetic separators are a critical solution, strategically positioned at processing points such as jacketed chocolate and syrup lines, bulk ingredient discharges, ingredient bag dump areas, and upstream of powder sprinkling systems. To protect product integrity and ensure safety, magnets should be installed at ingredient intake points and key locations throughout production, ideally placed upstream of final metal detection systems for comprehensive contamination control.
Consider the following when considering the appropriate magnets for dairy products:
- When used on sticky products, it is essential to ensure the configuration and cleaning methods or mechanisms won’t bind up or be affected by residual.
- Can the magnet be easily and safely accessed for cleaning?
- Does the working temperature of the magnets suit the application?
- Is the magnet design sanitary and compliant?
- Does the separator assembly comprise of high grade magnetics (such as RE80®) to ensure longevity and maintaining of magnet strength?
- What design criteria is in place to ensure effective magnetic separation is achieved without blockages?
- What means are taken to ensure magnet strength is maintained over time?
- Does the magnet comply with current HACCP and best practice standards (e.g. 0909MAGSEP 2-2021)?
- Is the magnet supplied with adequate certification?
Applications include:
- Sugar
- Salt
- Gluten
- Chocolate
- Potato chips
- Candies/Lollies
- Chewing Gum
- Cocoa powder
USDA Acceptance
Magnattack received a USDA Dairy Acceptance Certification in 2015 for special models of the Mag-Ram® Self Cleaning Separator, Rapidclean® Drawer Magnet, Round Pipe Separator, and the Powder Transfer Magnet. In 2019, the Emulsion & Slurry Pipeline Separator also received the USDA Acceptance Certification for use in dairy and sensitive liquid applications, as well as meat and poultry applications.
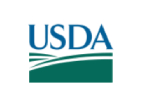
Trusted by Industry Experts
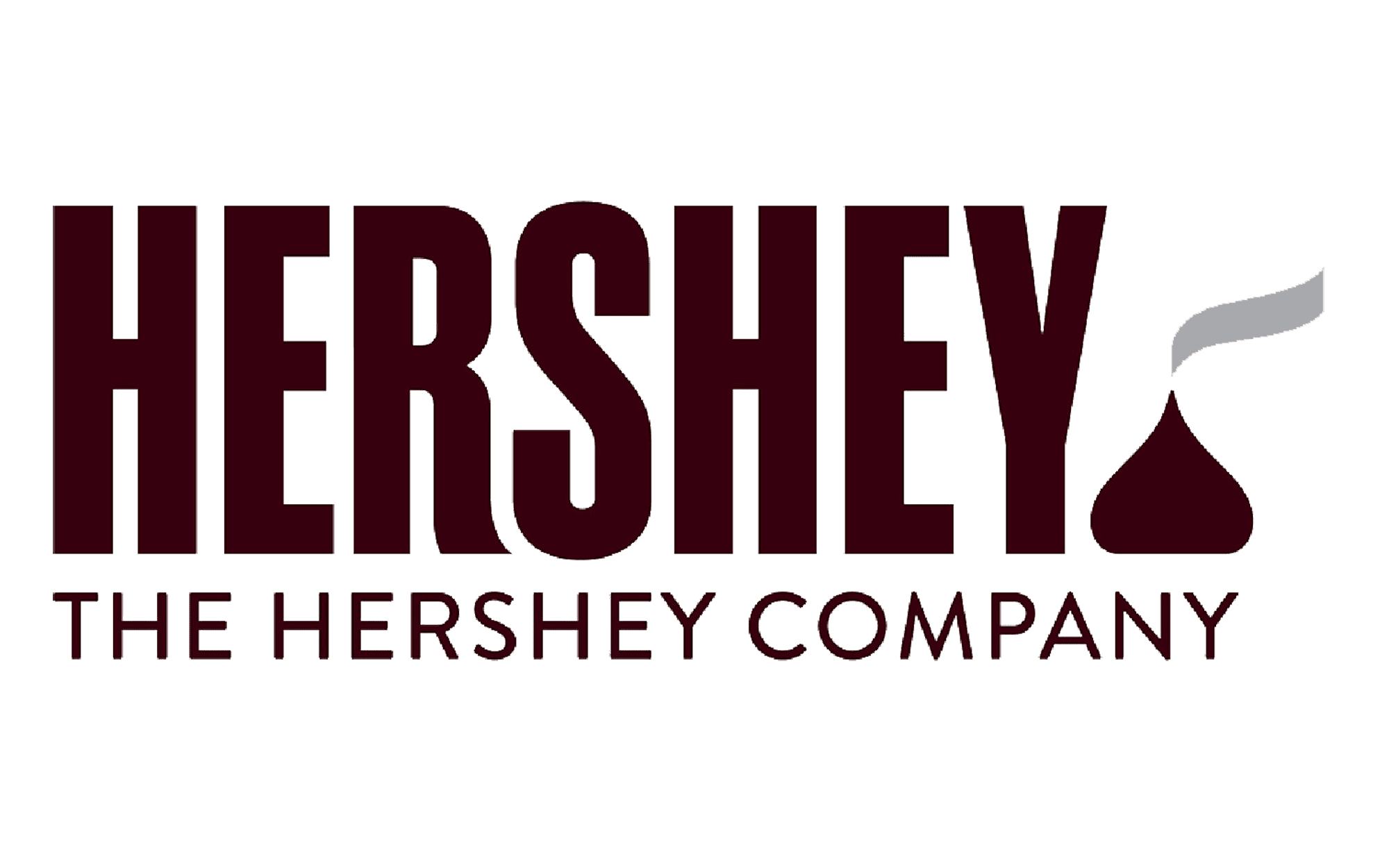
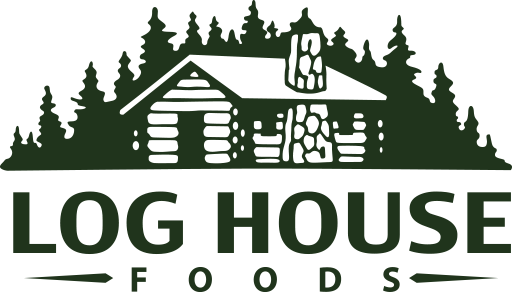
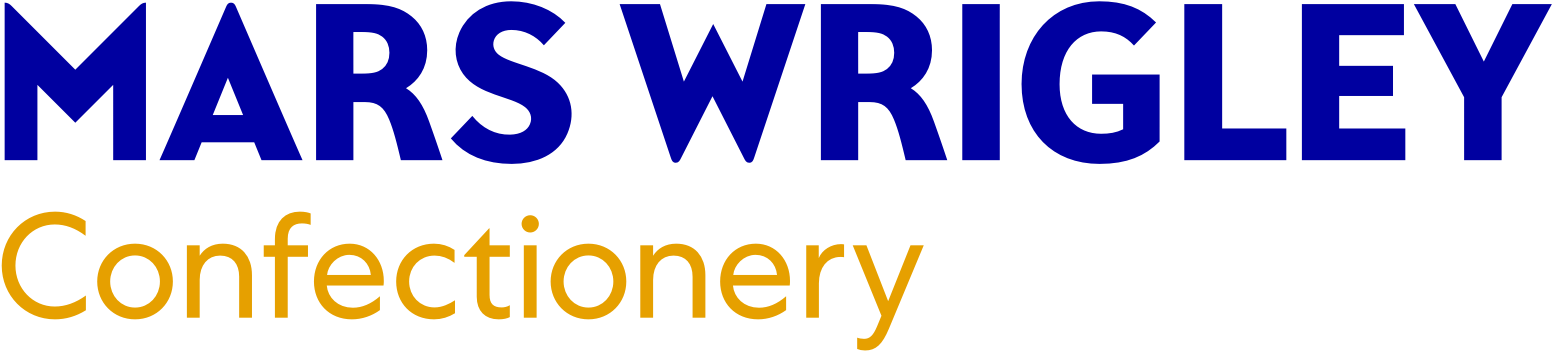
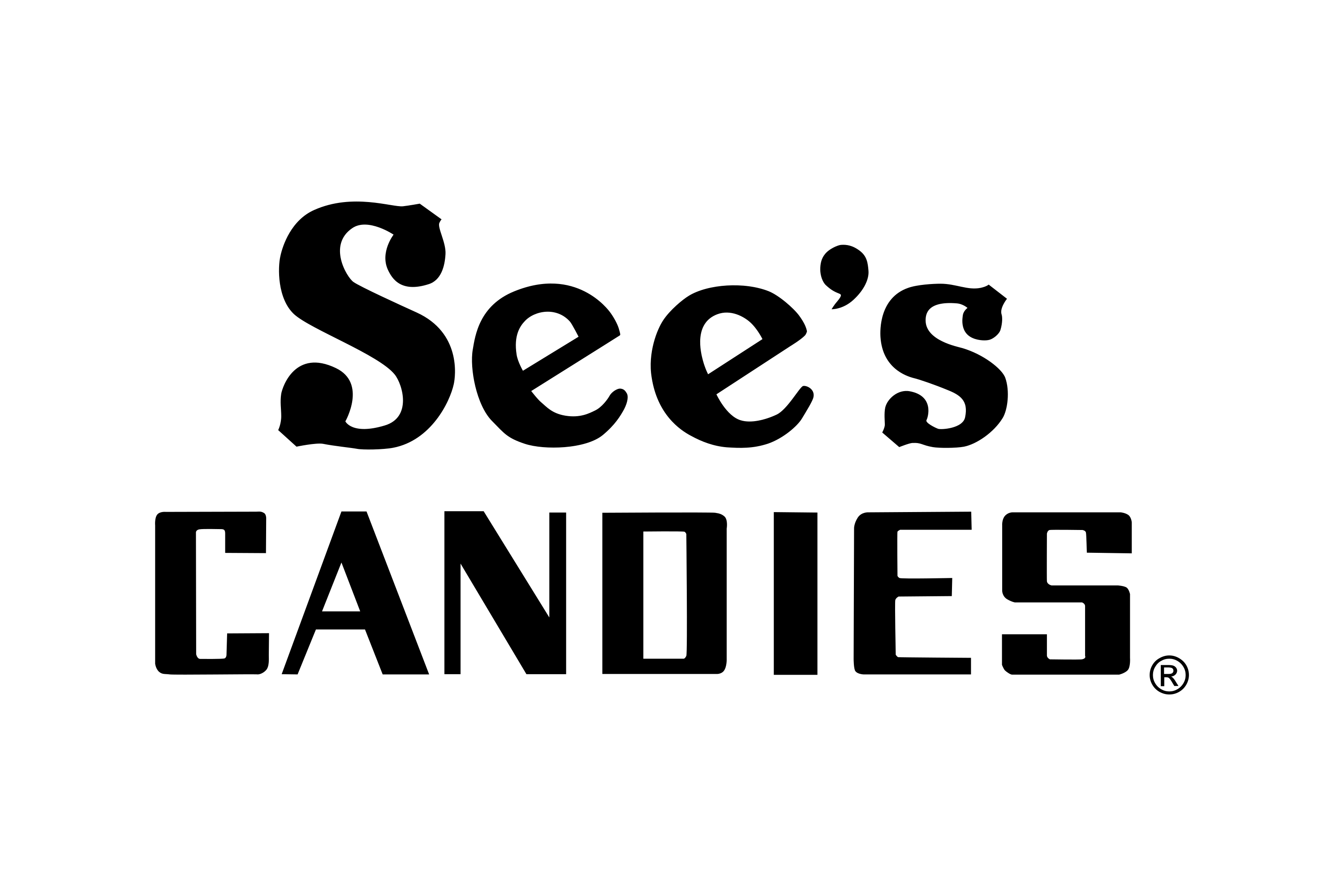
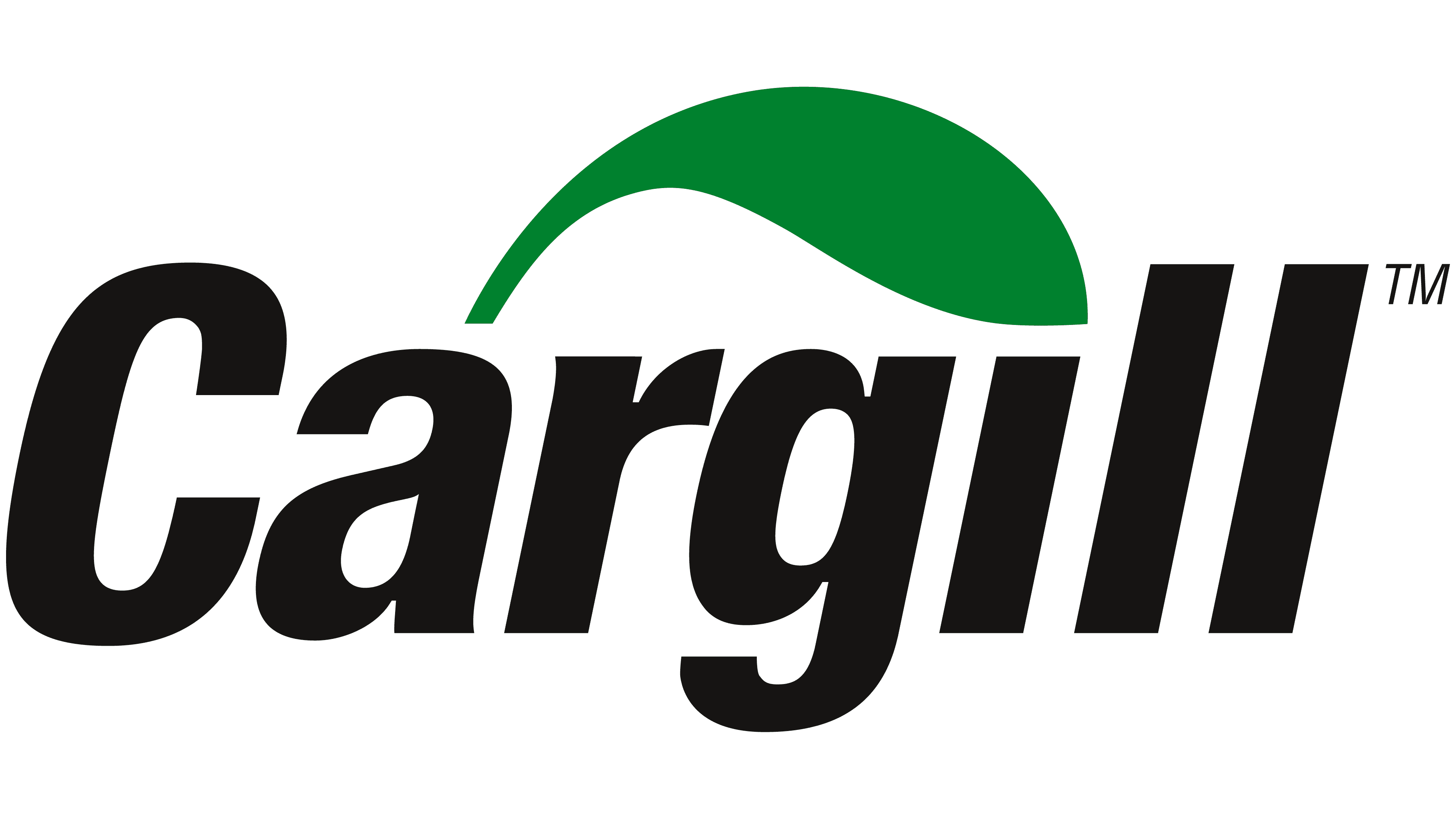
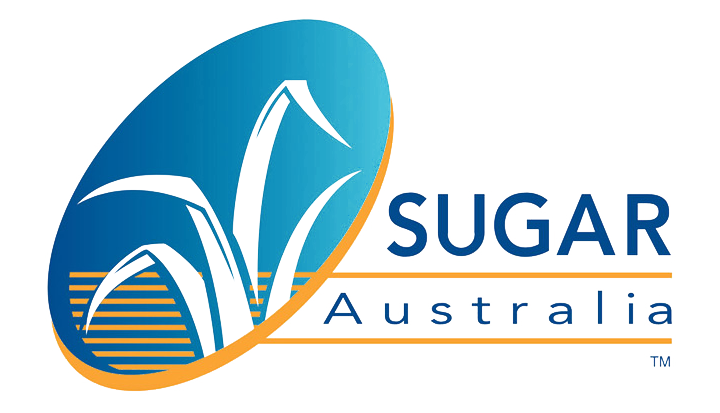
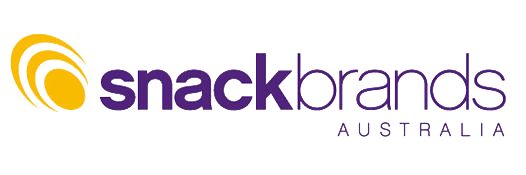
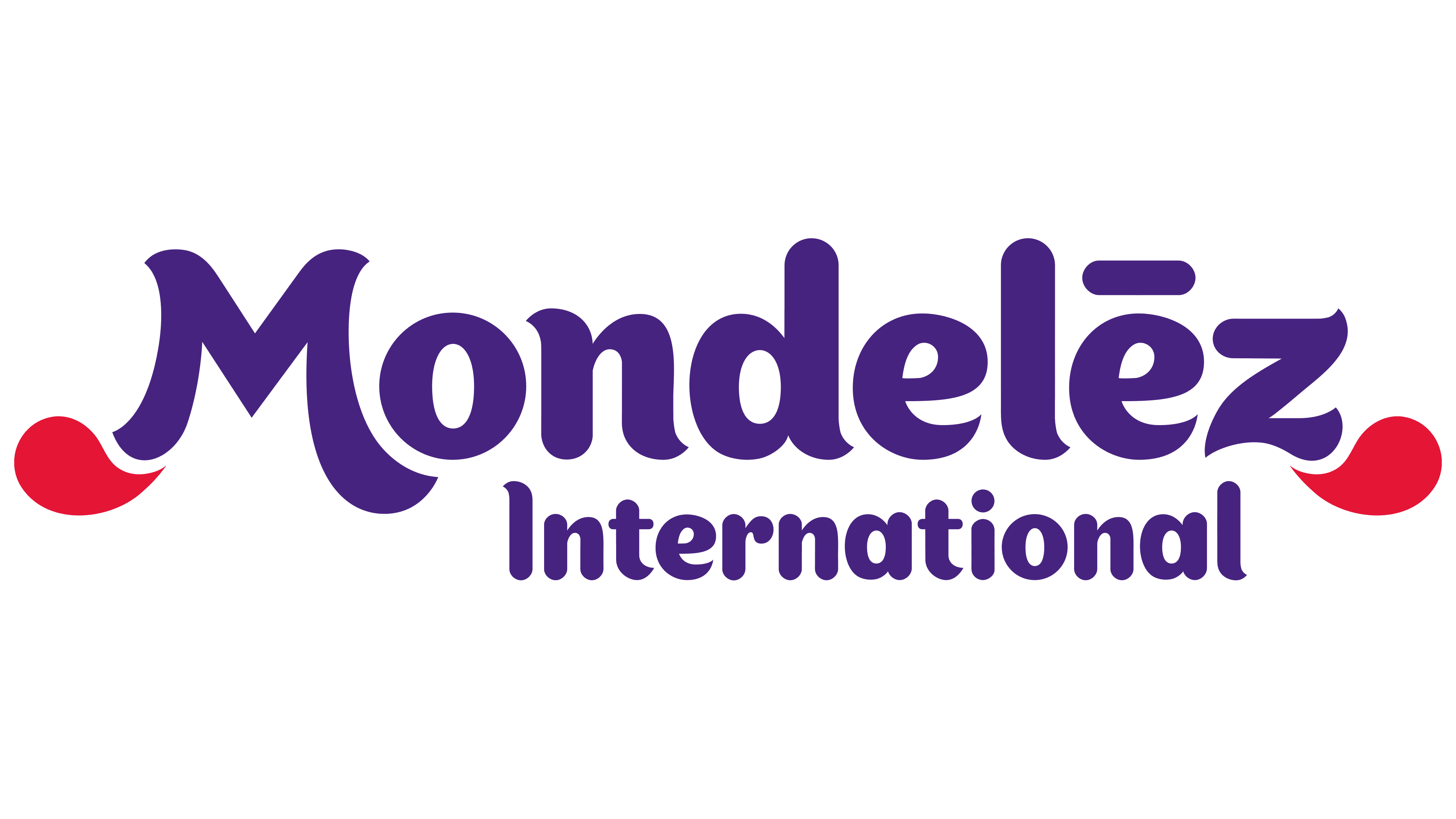
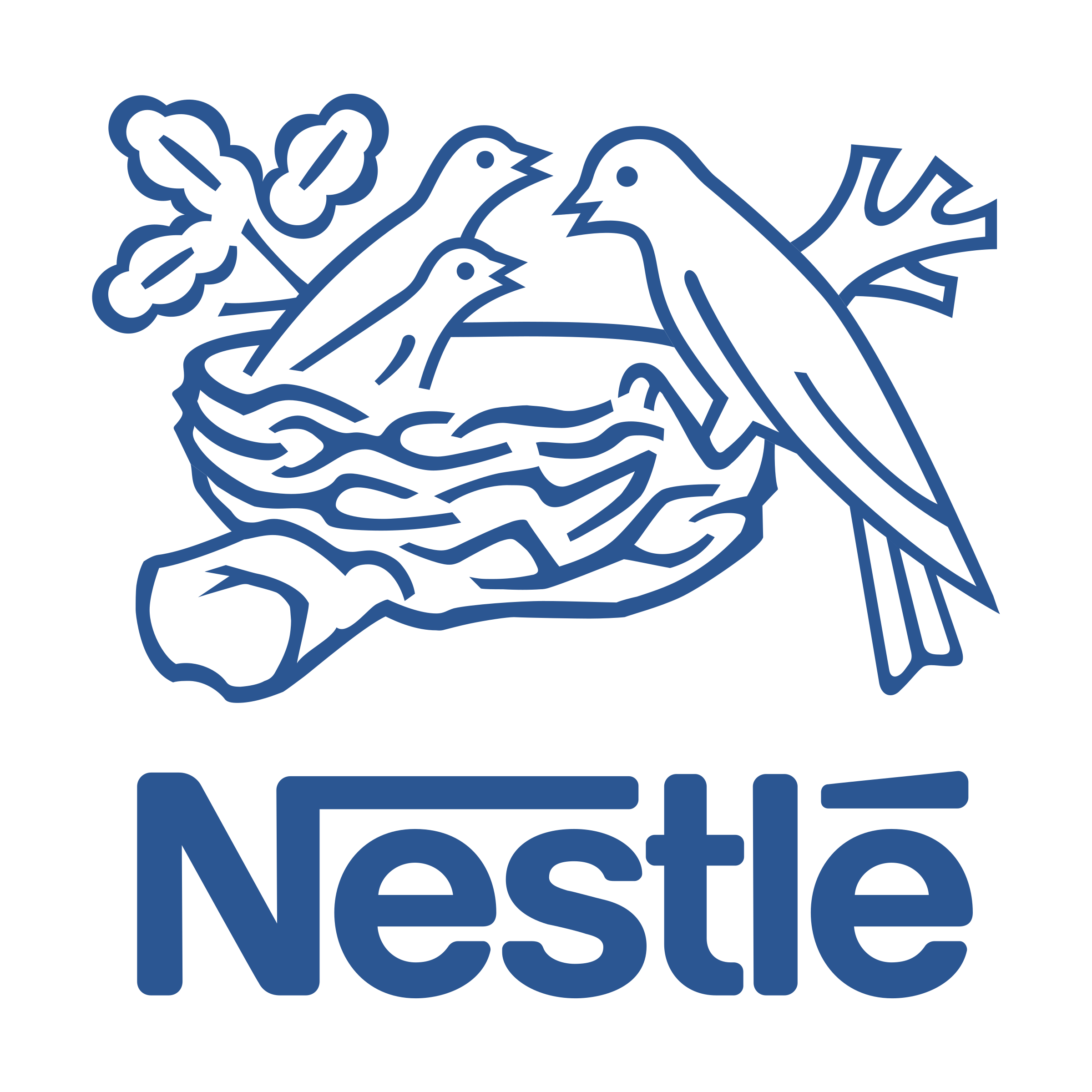
Talk to an Expert
Got a question or need a quote? Our Magnattack experts are here to offer fast, personalized guidance for all your magnetic separation needs. Simply fill out the form below, and one of our specialists will quickly reach out to assist you.